Partnering with Acción Performance allows your business to remain agile as production needs shift. Our customized Insourcing Vs. Outsourcing options eliminate wasted resources by optimizing performance as we seamlessly integrate into your logistics processes.
Our Insourcing Vs. Outsourcing Services
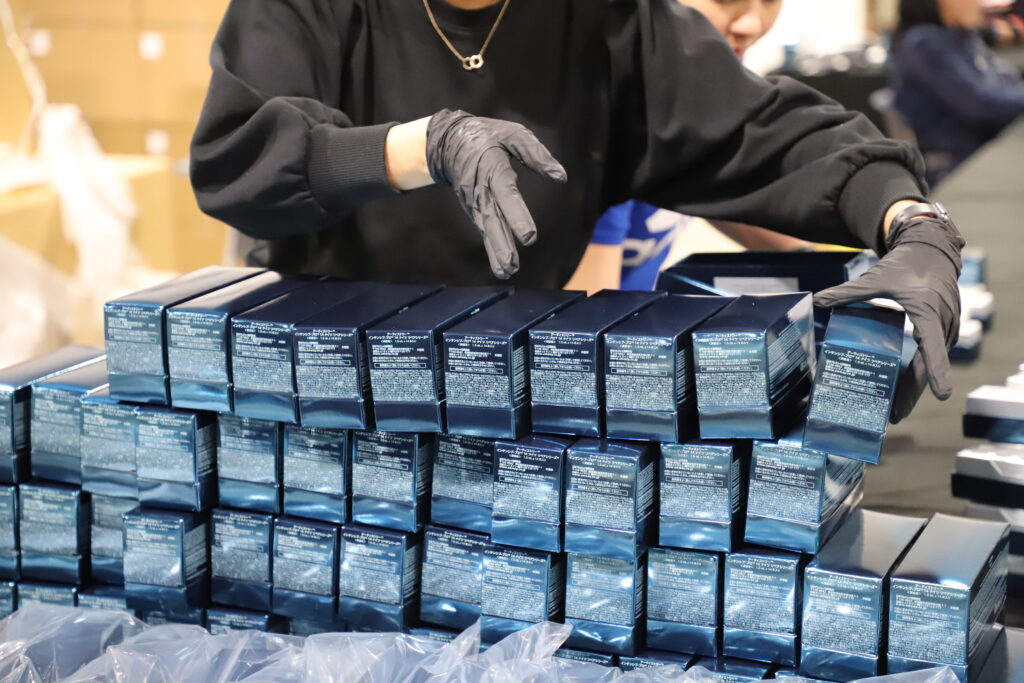
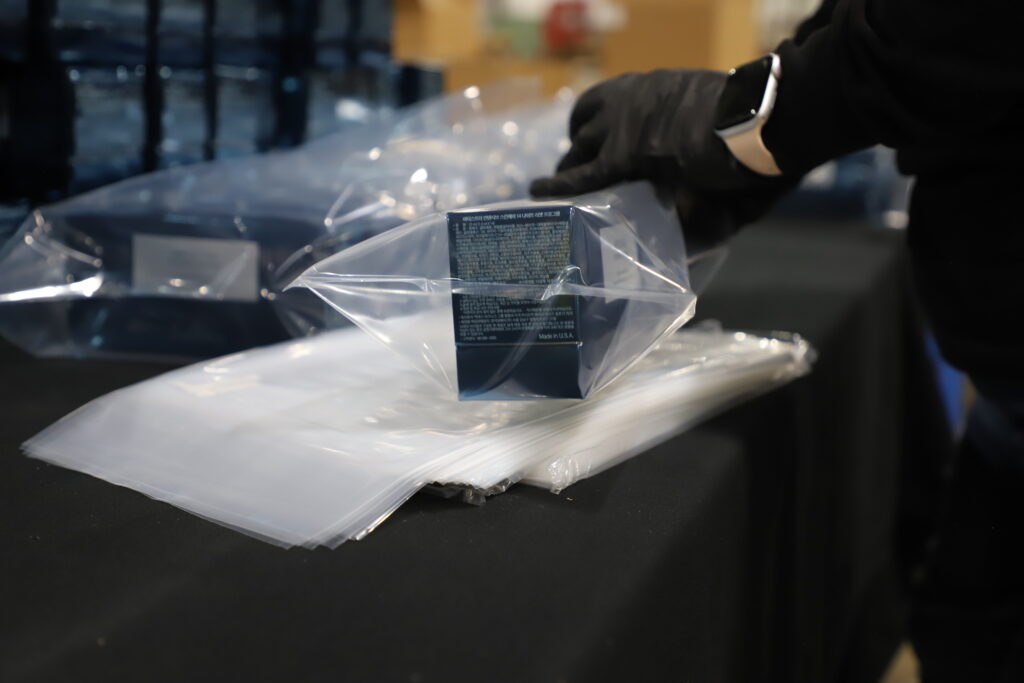
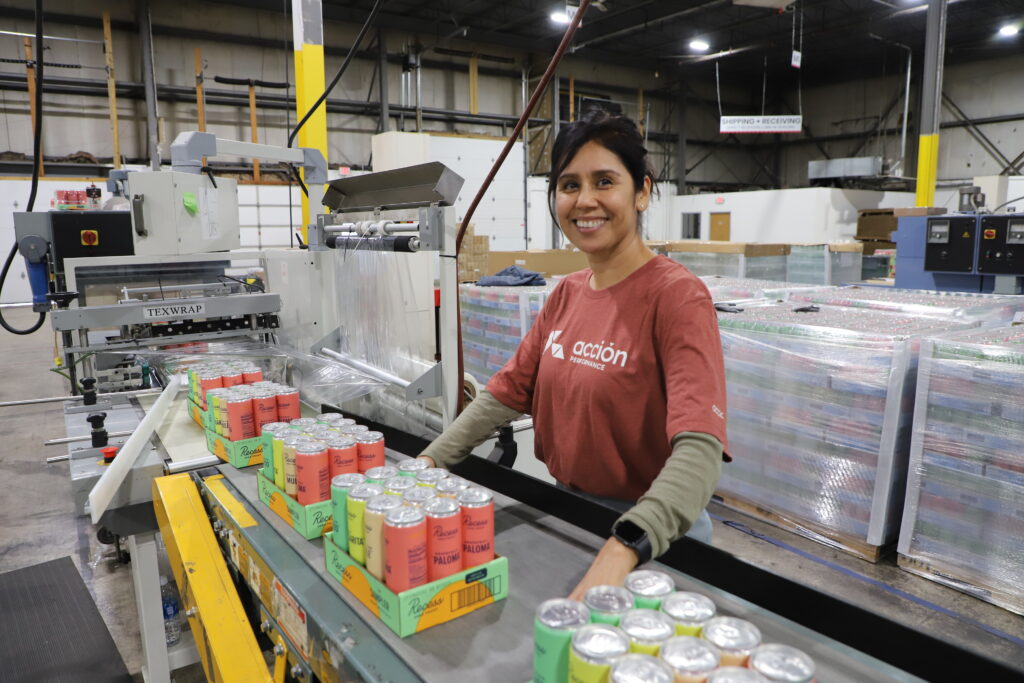
Packaging Solutions
Stay on top of product alterations and capitalize on packaging as a marketing tool to your clients. Our team can focus on product appearance while ensuring safe and secure delivery to its destination.
OUR CAPABILITIES
- Kitting & Assembly
- Labeling & Stickering
- Quality Inspection
- Sortation
- Repack & Rework
- Display Builds
- Returns Refurbishing
- Shrink Wrap & Secondary Packaging
- Fulfillment By Amazon (FBA) Prep
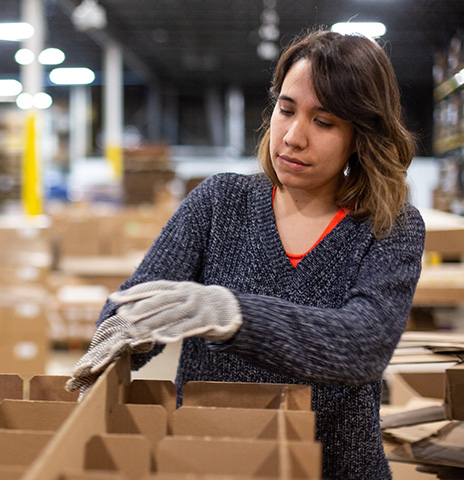
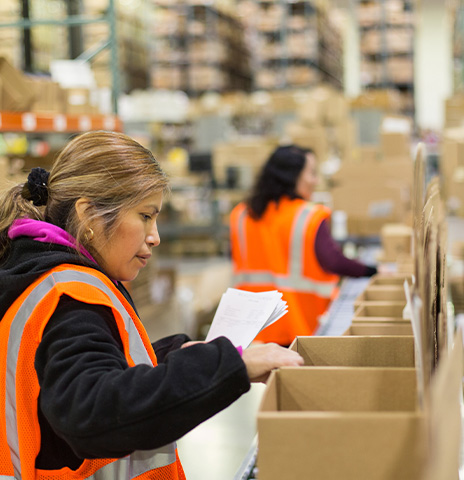
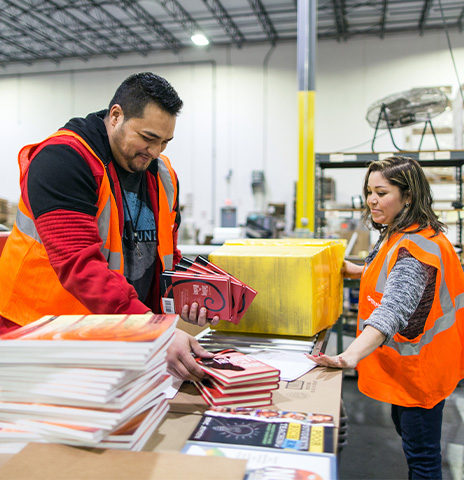
Assembly & Co-Manufacturing Solutions
Reduce overhead costs and boost speed to market by shifting your assembly and co-manufacturing tasks to the Acción team. Our skilled team prioritizes quality and safety at every step.
OUR CAPABILITIES
- Kitting & Assembly
- Labeling & Stickering
- Quality Inspection
- Sortation
- Repack & Rework
- Display Builds
- Shrink Wrap & Secondary Packaging
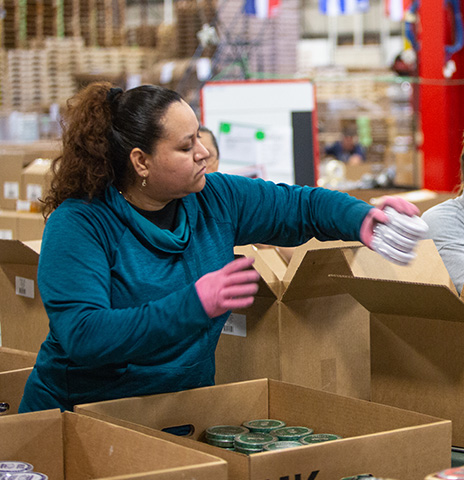
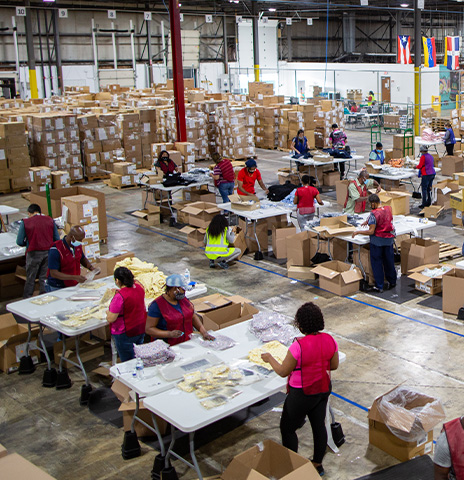
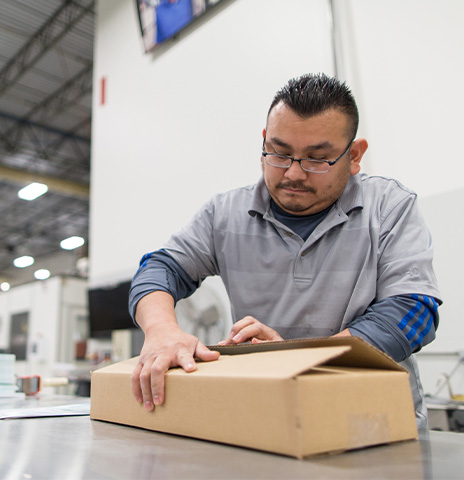
Fulfillment & Logistics Support
Improve efficiency and maintain client satisfaction by outsourcing key fulfillment operations. Our team leads will manage processes from pick and pack all the way to returns.
OUR CAPABILITIES
- Kitting & Assembly
- Labeling & Stickering
- Quality Inspection
- Sortation
- Repack & Rework
- Display Builds
- Returns
- Shrink Wrap & Secondary Packaging
- Refurbishing
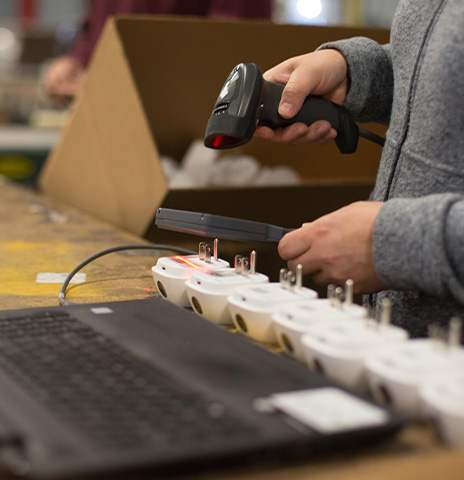
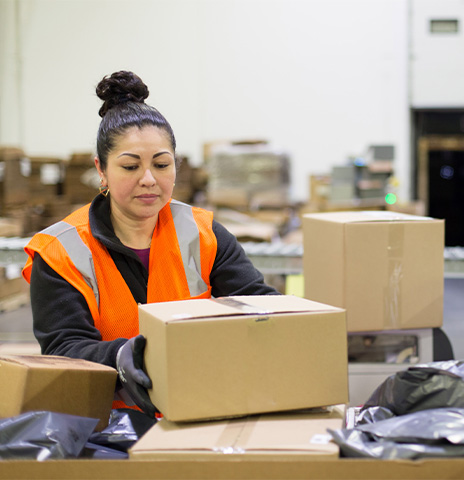
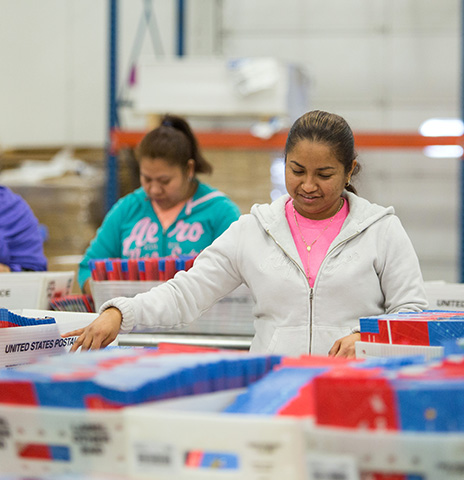
Fulfillment by Amazon (FBA) Prep
Ensure your products are properly packaged and sent on time for Fulfillment by Amazon. Acción Performance prepares your items to fit necessary requirements, saving your team extra time and valuable resources.
OUR CAPABILITIES
- Kitting & Assembly
- Labeling & Stickering
- Quality Inspection
- Sortation
- Shrink Wrap & Secondary Packaging
- Repack & Rework
- Packaging Solutions
-
Packaging Solutions
Stay on top of product alterations and capitalize on packaging as a marketing tool to your clients. Our team can focus on product appearance while ensuring safe and secure delivery to its destination.
OUR CAPABILITIES
- Kitting & Assembly
- Labeling & Stickering
- Quality Inspection
- Sortation
- Repack & Rework
- Display Builds
- Returns Refurbishing
- Shrink Wrap & Secondary Packaging
- Fulfillment By Amazon (FBA) Prep
- Assembly &Co-Manufacturing Solutions
-
Assembly & Co-Manufacturing Solutions
Reduce overhead costs and boost speed to market by shifting your assembly and co-manufacturing tasks to the Acción team. Our skilled team prioritizes quality and safety at every step.
OUR CAPABILITIES
- Kitting & Assembly
- Labeling & Stickering
- Quality Inspection
- Sortation
- Repack & Rework
- Display Builds
- Shrink Wrap & Secondary Packaging
- Fulfillment &Logistics Support
-
Fulfillment & Logistics Support
Improve efficiency and maintain client satisfaction by outsourcing key fulfillment operations. Our team leads will manage processes from pick and pack all the way to returns.
OUR CAPABILITIES
- Kitting & Assembly
- Labeling & Stickering
- Quality Inspection
- Sortation
- Repack & Rework
- Display Builds
- Returns
- Shrink Wrap & Secondary Packaging
- Refurbishing
- Fulfillment byAmazon (FBA) Prep
-
Fulfillment by Amazon (FBA) Prep
Ensure your products are properly packaged and sent on time for Fulfillment by Amazon. Acción Performance prepares your items to fit necessary requirements, saving your team extra time and valuable resources.
OUR CAPABILITIES
- Kitting & Assembly
- Labeling & Stickering
- Quality Inspection
- Sortation
- Shrink Wrap & Secondary Packaging
- Repack & Rework
Our Capabilities
Don’t let capacity constraints keep you from reaching your operational goals. Acción Performance can quickly adjust our resources to get started on projects quickly, and exceed timeline expectations.
Managing Modern Solutions
Optimized supply chain solutions aren’t “one size fits all,” and neither are our pricing models. Our team
finds the best approach for your project to maximize your resources, including cost.
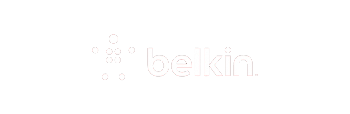
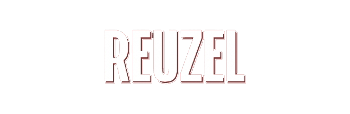
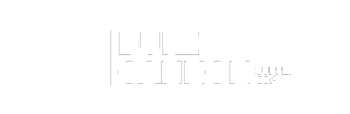
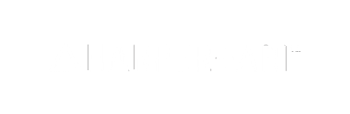
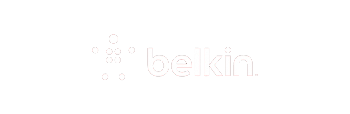
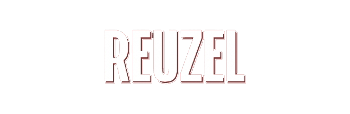
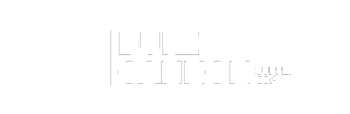
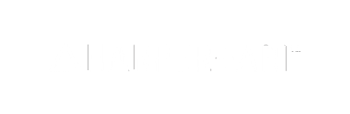
Custom Solutions
See how the Acción team creates individualized solutions for our clients across industries to optimize their unique demands.
Insourcing Vs Outsourcing
Most business owners and managers today have to weigh insourcing vs outsourcing when they require help with a project or their enterprise. These companies have to choose between hiring employees to complete the project internally or getting an external entity to do it for them. They will have to assess the benefits and drawbacks of each move to determine which most benefits them. Factors that they will evaluate to come to the decision include cost, security, and expertise, among others.
Understanding the difference between the two processes helps business leaders make the right choices that will benefit their firms in the long run.
Simply put, insourcing is using specialists in a company to complete a project. An insourcing synonym is inshoring, which you will see in other business texts. On the other hand, outsourcing is hiring experts outside the firm to complete the project.
There are several ways that businesses can perform outsourcing, and one of them is offshoring. Therefore, there is a difference between offshoring vs outsourcing, which business managers must know to do what is best for their companies.
Outsourcing is simply the process of hiring an individual or organization outside the company to perform various business processes or operations. Offshoring is when a firm outsources to a person or company outside of its country’s borders.
Outsourcing vs offshoring examples abide aplenty because many companies all over the world do it. If an American software company were to engage another American company to handle some of its processes e.g. customer support, it would be considered outsourcing. However, if the American company hires a Mexican or Indian company, it is considered offshoring.
Therefore business executives evaluate offshoring and outsourcing advantages and disadvantages and then choose which avenue to use.
What is insourcing vs outsourcing? Read on to find out.
What Is Insourcing?
So, what is insourcing and how does it work? Insourcing is the practice of a company delegating various jobs, tasks, processes, or projects to teams or individuals within the firm instead of an outside source. The main reason why a company performs insourcing is because they have the resources to perform the task or project internally. Other reasons may be to protect their intellectual property rights and avoid security leaks. Therefore, the answer to what is insourcing is simply performing various jobs in-house as opposed to externally.
Insourcing examples include a company hiring foreign nationals with a specific skill set temporarily to perform a particular task. Another example is a firm working with an internal product team to develop a new product line instead of outsourcing the job.
Businesses seriously consider insourcing advantages and disadvantages before making their decision. Advantages of insourcing include alignment with company culture and values, developing internal team & expertise, and fewer communication and cultural barriers.
Disadvantages of insourcing include being more expensive to hire external teams, higher risk regarding legal and regulatory compliance as well, and restricted access to external expertise.
Do you want to learn what is insourcing in supply chain management? Keep reading.
Insourcing In Supply Chain Management
Having an in-house supply chain management is a big decision as most companies choose to outsource. However, insourcing in supply chain management is a good idea if you have a team that you believe can comfortably do the job while the company remains profitable. Doing so is usually more expensive to the company because it often involves starting a new department or implementing new processes in the firm.
However, there are several advantages of insourcing in supply chain management. One of them is increased quality control, meaning firms can ensure the highest standards for their products and services.
Another major benefit is that the talent is aligned with company values because firms use employees who share their vision and participate in the company culture. With more control and visibility into operating costs, firms can identify and rectify inefficiencies that are hurting their bottom line. There may also be state tax incentives for companies that hire local workers which improves profitability.
There are two main types of insourcing in supply chain management namely captive, where you hire employees permanently and project-based insourcing, where you hire employees for a project. Most insourcing examples will fit into the two categories.
Insourcing in supply chain management examples include a company having its own distribution center as opposed to hiring a 3PL partner.
A Company’s Approach To An Insourcing Vs Outsourcing Decision
A company’s approach to an insourcing vs outsourcing decision will depend on a multitude of factors. They will review insourcing vs outsourcing trends as well to see if there are developments that will benefit them. The main criteria will be evaluating insourcing vs outsourcing pros and cons.
We have already outlined insourcing advantages and disadvantages, but let us evaluate an insourcing example. Law firms are excellent examples of companies that regularly perform insourcing.
The companies hire paralegals in addition to legal software so they can perform all of their work in-house. Even though there are disadvantages of insourcing, the firm may choose to accept the hire cost for increased compliance.
The firm will also evaluate the disadvantages and advantages of outsourcing. The advantages include saving money, more flexibility, and increased access to specialized skills and expertise.
The disadvantages of outsourcing are less quality control, increased security risks, and more communication & cultural barriers.
A company’s approach to this decision will depend on the company and the nature of its processes. The firm’s management will also matter significantly as they are the ones who have to weigh the pros and cons of insourcing vs outsourcing.
Advantages Of Insourcing
As stated above firms must evaluate the advantages of insourcing against the advantages of outsourcing to determine which best suits the company. In comparing insourcing vs outsourcing, they will have to review aspects such as insourcing vs outsourcing logistics. The management will also have to ask themselves in an insourcing vs outsourcing situation which of the following courses of action will yield the best results. They will study various outsourcing and insourcing examples for information to draw accurate conclusions.
Since we have already outlined some insourcing advantages and disadvantages, let us consider some of the more unique advantages of insourcing. One advantage is that it promotes creativity and innovation because firms can evaluate a project throughout every stage. They can hence identify problems and create solutions for the benefit of the project.
Though most firms choose outsourcing for the perceived cost benefits, insourcing can be just as cheap. The cost will largely depend on who the company hires, how long they hire them for, and the job they will be doing. Because of increased quality control, insourcing can save a firm money because there is less likelihood of lawsuits, fines, fees, and other legal expenses from defective products. Therefore, more quality control ensures a higher quality product and a stronger brand.
Moving From Outsourcing To Insourcing
The decision to move from outsourcing to insourcing is a challenging one, especially for large firms that have been outsourcing for decades. Doing so can substantially improve a firm’s in a variety of ways. Companies must develop an insourcing transition plan that will ensure the move is beneficial.
The plan will include various aspects such as having clear goals on what the company needs, paying attention to soft skills, adapting new hires to the company culture, and seeing the candidates in action. It must also involve explaining insourcing vs outsourcing to employees and reviewing insourcing and outsourcing examples so they are fully on board with the transition.
There are several pros and cons of moving from outsourcing to insourcing. The pros include increasing a company’s ability to innovate, collaborate, and be flexible. On the other hand, the move can be quite expensive and could take time before the firm adapts.
The hardest part of the transition is the cost. The moving from outsourcing to insourcing cost will be significant and an insourcing vs outsourcing cost analysis excel will be necessary to outline all the details and keep the cost as low as possible.
Benefits Of Insourcing Vs Outsourcing
Before making the transition, it is paramount to evaluate the benefits of insourcing vs outsourcing. Only after the firm’s management determines that the benefits outweigh the drawbacks can the move be possible. One of the best ways to do this is to study as many outsourcing vs insourcing examples as possible.
Only by truly understanding the pros and cons of insourcing vs outsourcing manufacturing can business owners and managers make the best decision. In most cases, insourcing is better when the process or project is vital to the business and must be in-house for reasons such as compliance, risk, and company culture. On the other hand, outsourcing is better when tasks are not essential to the business, and a firm wants to save money or have access to a larger talent pool.
One of the most integral aspects of the shift from outsourcing to insourcing is the cost. Therefore, the company’s management must conduct an insourcing vs outsourcing cost analysis to see if the transition is beneficial.
The cost analysis will have to take into account the short-term and long-term needs of the business. Though the short-term expense may be high, the long-term cost of the transition may be lower than its benefit.
Learn more about Insourcing and Outsourcing in Supply Chain Management.