Collaborating with Acción Performance in Indianapolis, Indiana, ensures your business can swiftly respond to evolving kitting and assembly demands. Our tailor-made kitting and assembly solutions are designed to boost efficiency, reduce waste, and seamlessly align with your logistics operations.
Kitting and Assembly in Indianapolis, Indiana
Welcome to Acción Performance: Your Premier Kitting and Assembly Partner in Indianapolis, Indiana
At Acción Performance, we excel in reshaping kitting and assembly solutions for businesses in Indianapolis and the surrounding areas. Driven by our unwavering commitment to excellence and innovation, we are dedicated to enhancing your supply chain and production processes.
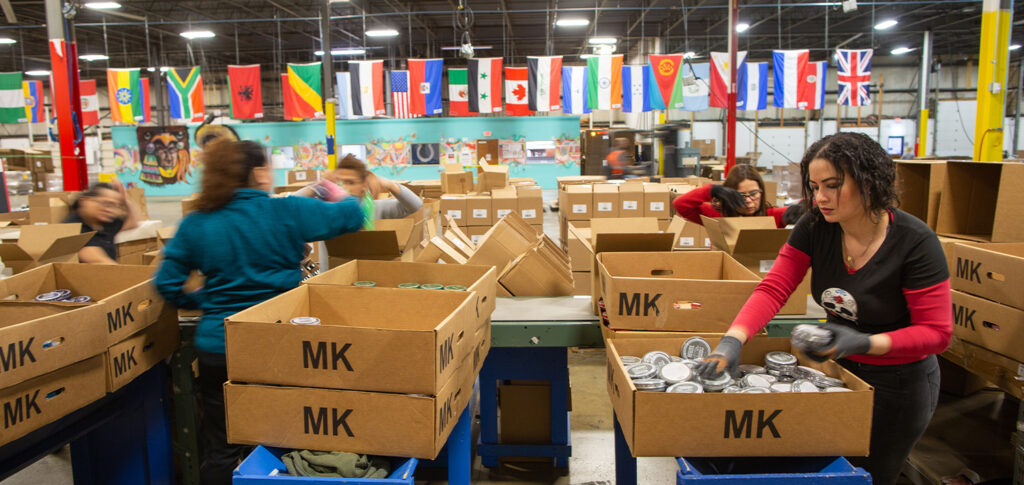
We Check All of Your Boxes:
Strategic Locations
At Acción Performance, we take pride in our strategic location at the heart of Indianapolis, Indiana. Our central positioning is instrumental in providing businesses across the region with efficient and cost-effective kitting and assembly solutions.
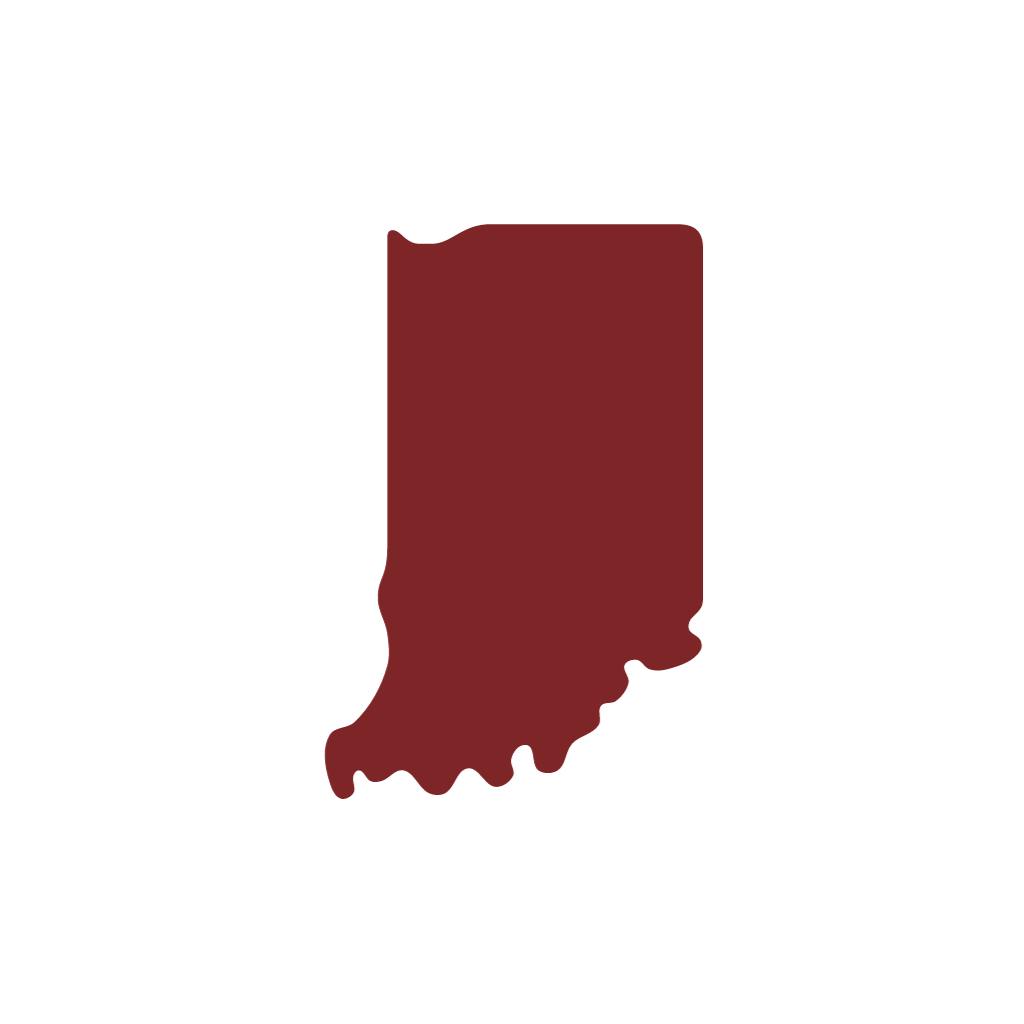
Solutions Where You Need Them
We understand business needs from all industries. Our team is equipped to work when and where you need us.
Insourcing
Extend Your Capabilities:
Unlock the power of seamless integration as our expert team integrates directly into your facility. We bring specialized skills, adaptability, and unparalleled expertise right to your doorstep.
Adaptive Solutions:
Every facility has unique needs. Our team is trained to quickly adapt to diverse environments, ensuring a smooth transition and immediate productivity.
Assured Quality & Compliance:
Our team is trained to adhere to the highest standards of quality and compliance. Working within your facility, we’ll uphold and reinforce your brand’s reputation for excellence.
Outsourcing
Harness Our Team’s Skills:
Bring your projects to our facility, and our dedicated team will handle them with unmatched precision and skill. We offer a harmonious blend of your vision and our executional brilliance.
Seamless Integration:
Our team swiftly adapts to your specific requirements and methodologies, ensuring a seamless transition and continuity in your project outcomes.
Optimized Outcomes:
Our team, seasoned in diverse projects, ensures that your tasks are executed with efficiency, accuracy, and a commitment to the highest quality standards.
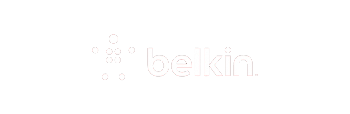
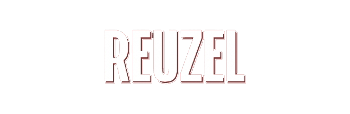
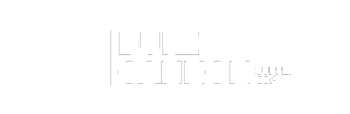
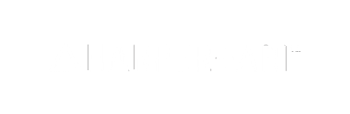