Partnering with Acción Performance allows your business to remain agile as production needs shift. Our custom order picking warehouse solutions to eliminate wasted resources by optimizing performance as we seamlessly integrate into your logistics processes.
Order Picking Warehouse
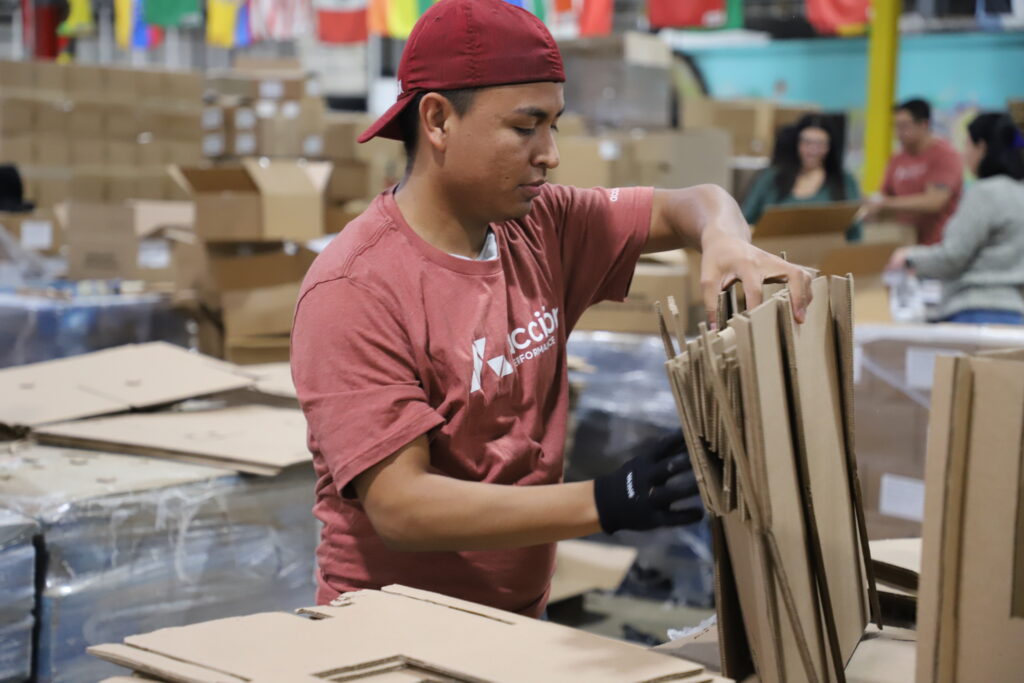
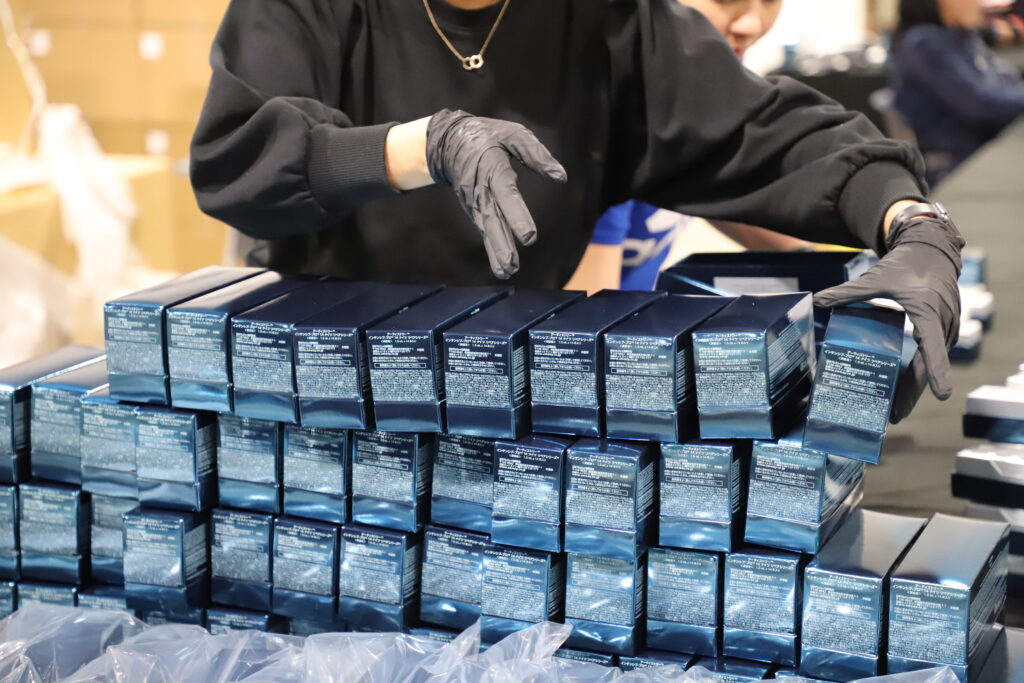
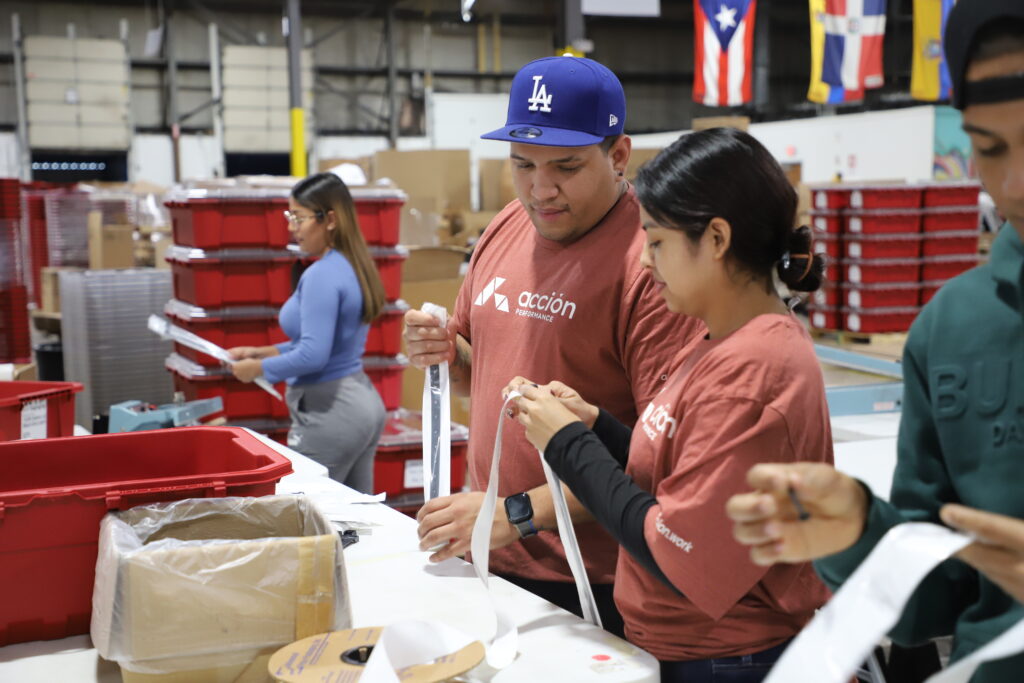
Packaging Solutions
Stay on top of product alterations and capitalize on packaging as a marketing tool to your clients. Our team can focus on product appearance while ensuring safe and secure delivery to its destination.
OUR CAPABILITIES
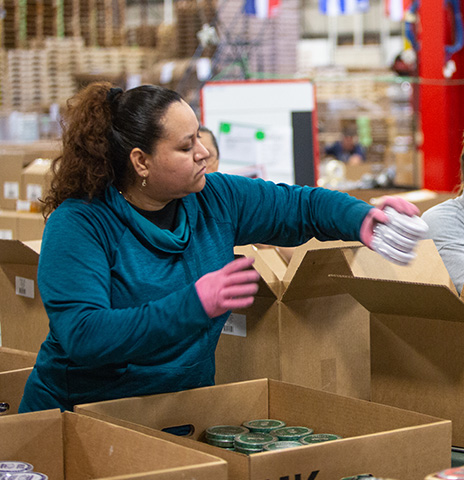
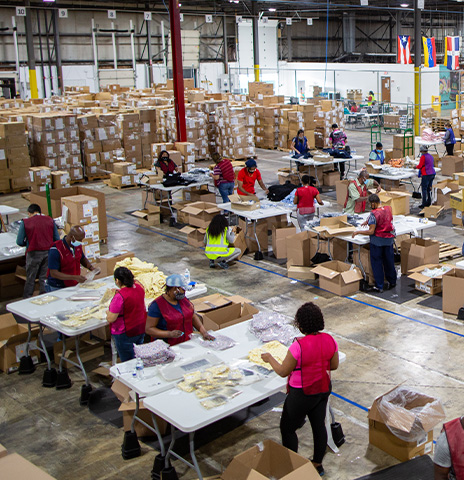
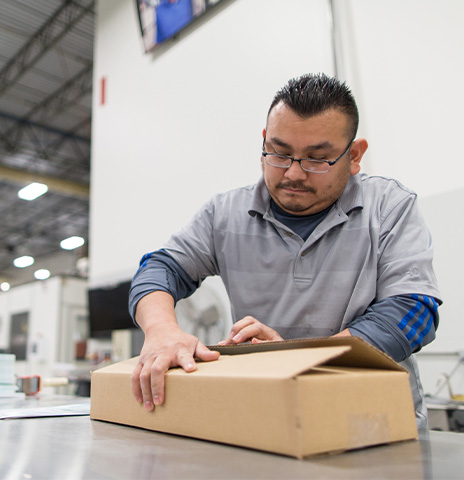
Fulfillment & Logistics Support
Improve efficiency and maintain client satisfaction by outsourcing key fulfillment operations. Our team leads will manage processes from pick and pack all the way to returns.
OUR CAPABILITIES
- Kitting and Assembly
- Primary and Secondary Packaging
- Shrink Wrap
- Labeling and Stickering
- Sortation
- Repack and Rework
- Display Builds
- Returns
- Refurbishing
- Packaging Solutions
-
Packaging Solutions
Stay on top of product alterations and capitalize on packaging as a marketing tool to your clients. Our team can focus on product appearance while ensuring safe and secure delivery to its destination.
OUR CAPABILITIES
- Fulfillment &Logistics Support
-
Fulfillment & Logistics Support
Improve efficiency and maintain client satisfaction by outsourcing key fulfillment operations. Our team leads will manage processes from pick and pack all the way to returns.
OUR CAPABILITIES
- Kitting and Assembly
- Primary and Secondary Packaging
- Shrink Wrap
- Labeling and Stickering
- Sortation
- Repack and Rework
- Display Builds
- Returns
- Refurbishing
Our Capabilities
Don’t let capacity constraints keep you from reaching your operational goals. Acción Performance can quickly adjust our resources to get started on projects quickly, and exceed timeline expectations.
Managing Modern Solutions
Optimized supply chain solutions aren’t “one size fits all,” and neither are our pricing models. Our team
finds the best approach for your project to maximize your resources, including cost.
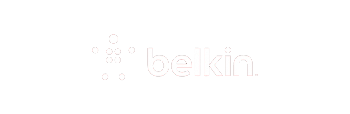
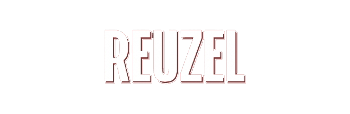
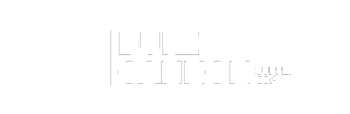
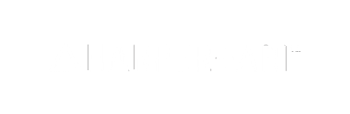
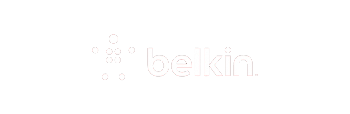
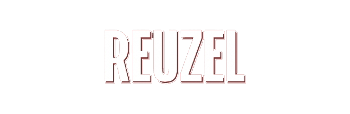
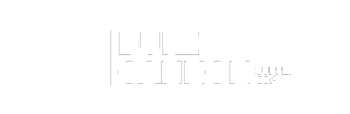
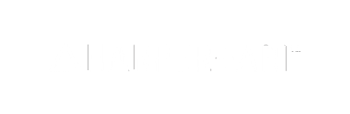
Custom Solutions
See how the Acción team creates individualized solutions for our clients across industries to optimize their unique demands.
Order Picking Warehouse
An order-picking warehouse is a facility where workers (or automated robots) pick items from bulk supplies to fulfill a customer purchase and shipping action. Modern retailers like Walmart and Target depend on picking warehouses for logistics purposes. Amazon calls these warehouses fulfillment centers because they satisfy customer requests for quick delivery. Along with supply chain logistics, picking is a product of customer requests to speed up deliveries. As a result, some picking warehouses provide same-day delivery.
An order-picking warehouse must be tuned into the retail marketers advertising schedules or risk catastrophic delays in product delivery. To this end, order-picking strategies should be streamlined so that bulk products get delivered with the least turnaround time. A tight and efficient bulk delivery schedule provides the best opportunities for expedited deliveries. It also cuts down on warehouse storage of unsold items because the supply side is tighter and with fewer overstocks.
Order-picking strategies can be streamlined with advanced logistics planning and automation. This leads to an impetus that warehouse workers can be replaced to a certain degree with picking robots. As the online marketplace revolution continues, artificial intelligence and smart picking robots will enhance warehouse work, not replace it.
In the future, the picking types will depend on the product and how much of the process can be automated. The inside of an order-picking warehouse will change with future technology developments.
Picking warehouses are not a new retail development but are evolving as the twenty-first-century rolls on. These warehouses serve as disruptive tools that decrease the importance of traditional package delivery. As such, today’s warehouse pickers could one day be logistics experts by understanding the picking warehouse strategies that can be used for special product delivery. This promotes outside-the-box thinking and helps tomorrow’s managers and CEOs work in a tech-driven industry.
Order Picking Example
One way of showing what an order-picking warehouse does comes from a picking example. Picking warehouses are designed for the efficient collection of individual products to support the fulfillment of customer purchases. Therefore, the importance of the picking process in warehouse cannot be downplayed. Every split second matters as computer programmers look for ways to improve logistics planning.
For example, an order for groceries comes in with requested products spread throughout the store. A warehouse picker can’t just walk over and choose the first product on the list without a plan in place that minimizes the distance between items. If there are three items on a list from the same area, the picker should choose those items and then go to the next cluster of items. Consequently, this picking example is commonplace among picking strategies where a shopper picks groceries for a client.
The preceding order picking example shows the importance of the picking process in warehouse settings. Any order-picking definition should include an impetus to save time while refining the logistics. This impetus should go from the top manager position all the way to the warehouse pickers, as logistics planning creates strategic business opportunities the entire company prospers from.
In contrast to the cluster picking example of picking items for multiple orders in the same zone, the single order picking example gets scheduled according to its position in the queue. A warehouse worker will pick up single-order shipments per customer, not according to the zone. Instead of picking multiple products from different orders in the same zone, single-item customers get picked according to zone placement and other fulfillment requests.
Order Picking Equipment
When barcode scanners hit the market, warehouse pickers everywhere relaxed a bit. Finding and shipping customer purchases got a massive boost of time-saving ROI. But barcode scanners were just the beginning of advanced logistics planning. Today’s technology supports order-picking equipment and automated order-picking systems that can almost eliminate people. But not quite. Order-picking equipment needs occasional maintenance. Conversely, technicians will always need to be employed to run and maintain the systems.
Order picking is the most labor-intensive part of logistics planning. This is why major retailers like Walmart and Amazon invest in AI that improves order-picking systems. These systems are crucial time-consuming improvement points. Instead of warehouse workers running around as fast as they can picking orders, they are better served by understanding and running the warehouse picking systems created for automation. This is because warehouse picking time standards are one of the last remaining improvement points for order-picking equipment development and corresponding strategies. Asking the question of how to improve warehouse picking speed and accuracy should lead to small details that could add up to several minutes of saved time.
Order picking equipment should be managed to improve warehouse picking time standards that increase the buyer’s positive experience. These systems can be modified for combinations of single-order picking and clustering due to warehouse picking time standard improvements. They can also be programmed with customer service as a priority.
Order Picking Process
Without question, the order-picking process helps answer the question – how to improve warehouse picking speed and accuracy? In addition to clustering and single-order warehouse picking, batch picking might help improve picking speed. Batch picking comes in single batch pick or multiple batch picking.
Batch picking collects all customer SKUs and works out the quickest way to fulfill the entire order. The warehouse worker or the automated system minimizes travel time between product retrievals. Whereas warehouse workers typically use tiered carts for product retrievals according to a specific route, batch picking with an automated system sees the whole picture. It can make small changes that cut a few seconds here and there that eventually add up. Manual warehouse picking doesn’t have the same fine-tuning detail. Manual is okay for single-order picking without a complicated warehouse layout.
From batch picking to clustering and single order picking, the days of manual warehouse picking could be numbered. As technology improves, the importance of the picking process in a warehouse setting becomes an ever more sophisticated move to cut split-seconds from logistics planning.
As picking systems improve, the need for single-order picking becomes obsolete in a fully automated system.
Average Warehouse Pick Rate
The warehouse picking industry measures their work with an average warehouse pick rate. Calculate by dividing the hours worked by the total orders picked for an hourly pick rate. Pick rate is an important aspect of the industry because the precise role automation and AI will play in efficiency can be lost in human hands.
Thus, if warehouse worker wants to increase their pick rate, they should at least think like a picking system and cut seconds here and there. Unfortunately, people need things like bathroom breaks picking robots doesn’t.
Average warehouse pick rates also apply to online grocery pickup (OGP), a process that gained popularity during the pandemic. Because OGP is client-focused on pick-up times, answering the question “how is ogp pick rate calculated” might be confusing. To begin, OGP rates are quicker without frozen or perishable foods. Accordingly, each OGP retailer has different processes so it’s best to stay within an OGP system and not compare them to each other. If you want answers on how to be a faster warehouse worker and how to improve your pick rate, ask supervisors for guidance.
Warehouse industry statistics show Walmart with a dominant share of OGP business. Thus, warehouse picking time standards for Walmart are different from Target. Walmart has its own picking productivity formula based on internal factors like the time it takes groceries to get to the curbside pickup zone.
Warehouse Picking Strategies
Warehouse-picking strategies help answer questions like how to improve warehouse-picking speed and accuracy. Small tweaks in strategy can produce substantial time saving with accumulation over time. Given technology’s reach into everyday life, warehouse picking time standards may be only adjustable using computer code.
As picking warehouses spread throughout the globe, will warehouse picking time standards continue to be as important to machines as they are to people? Conversely, can warehouse-picking strategies be standardized across multiple industries? Probably not and that’s the point of keeping pick rate formulas active, not just within one industry, but within one store like that can apply small tweaks across an entire OGP service force.
Single-order picking that focuses on one customer at a time, like Walmart’s OGP, can be improved for things like curbside waiting. But the same pick rate formula may not work for both a Florida and California Walmart because of cultural and other factors that don’t influence pick rates.
Warehouse Picking Systems
Like all other industrial systems, warehouse picking systems utilize information system technology that promotes efficiency. Batch-picking and multi-tiered batch-picking strategies could result from machine logic and artificial intelligence protocols. It could be that in the future, warehouse picking time standards result from computer programming and have little to do with human movements.