Partnering with Acción Performance allows your business to remain agile as production needs shift. Our customized Packing in Warehouse solutions eliminate wasted resources by optimizing performance as we seamlessly integrate into your logistics processes.
Our Packing in Warehouse Solutions
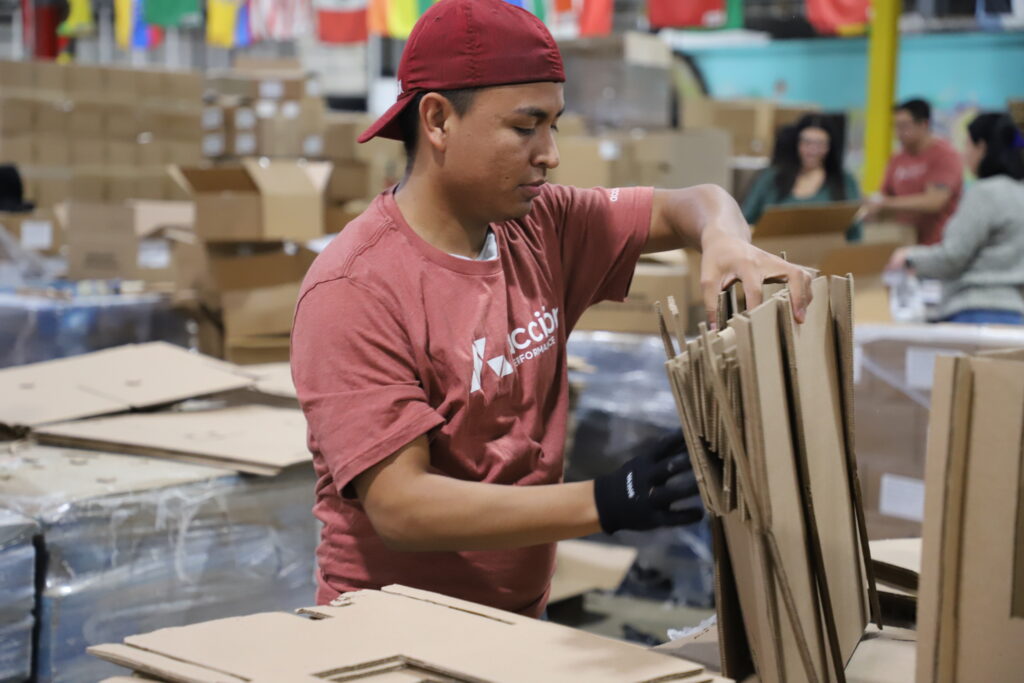
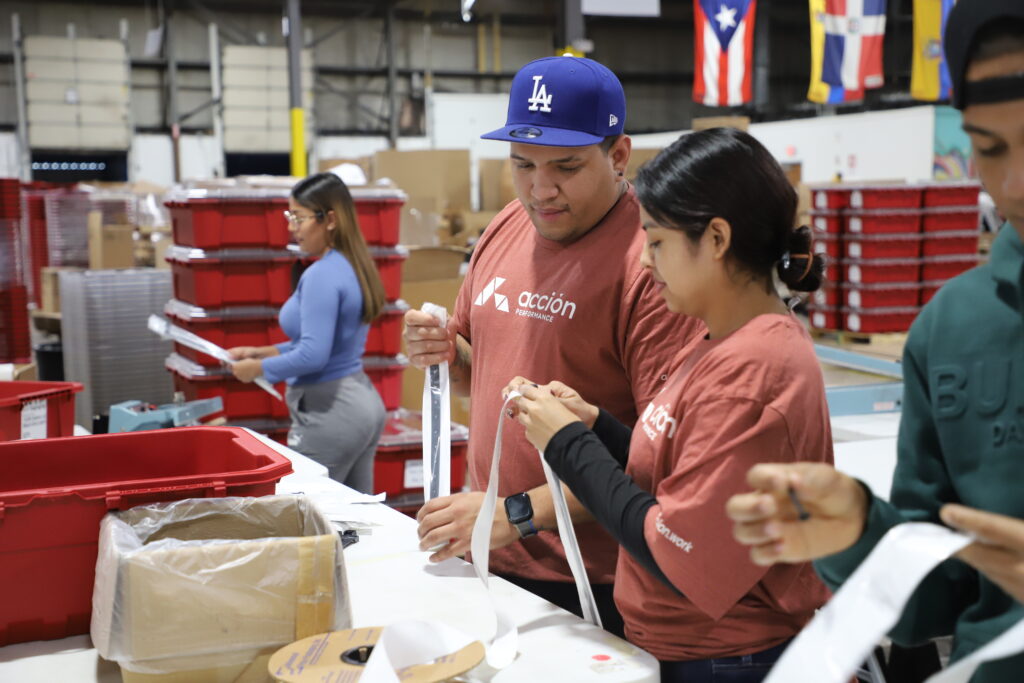
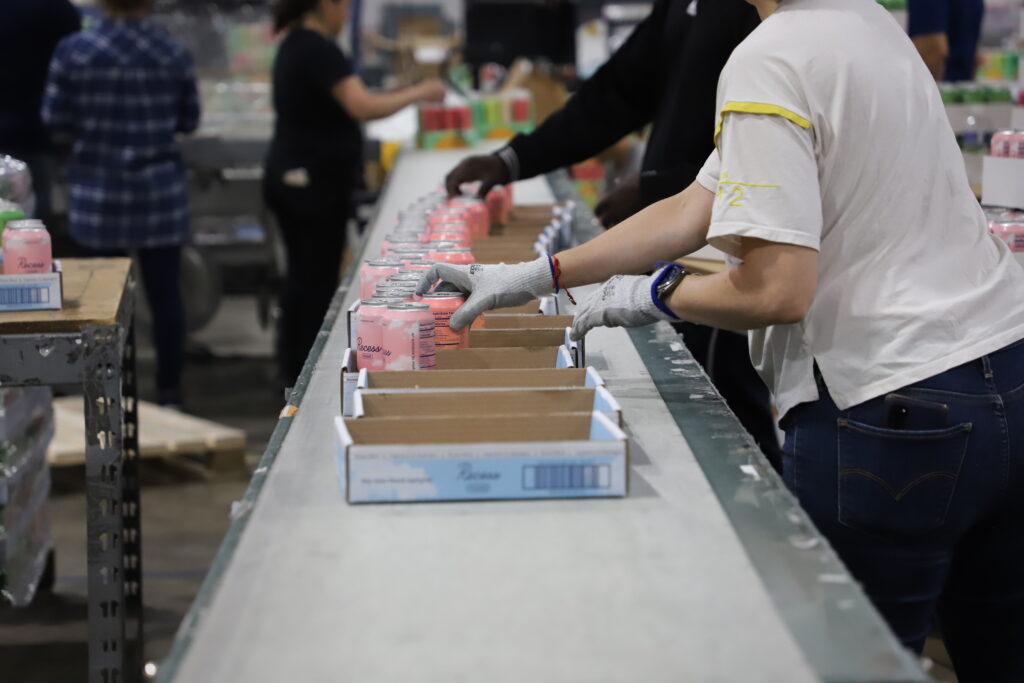
Packaging Solutions
Stay on top of product alterations and capitalize on packaging as a marketing tool to your clients. Our team can focus on product appearance while ensuring safe and secure delivery to its destination.
OUR CAPABILITIES
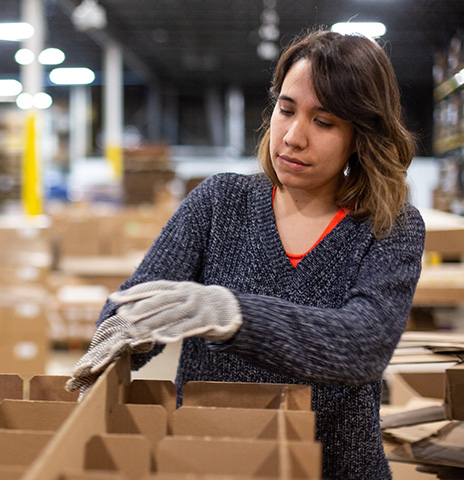
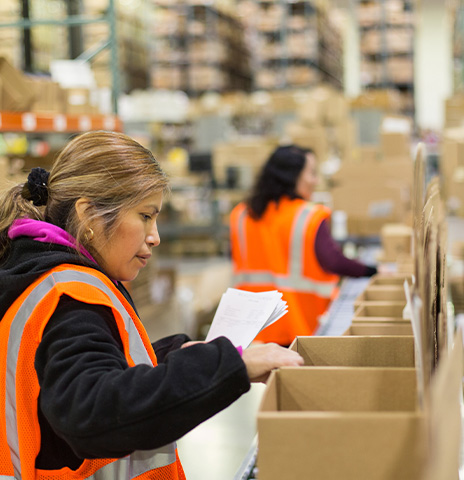
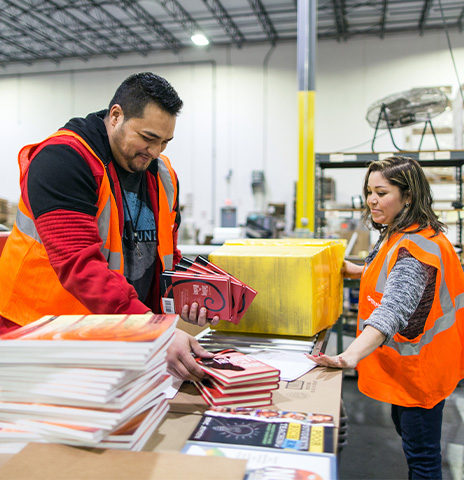
Assembly & Co-Manufacturing Solutions
Reduce overhead costs and boost speed to market by shifting your assembly and co-manufacturing tasks to the Acción team. Our skilled team prioritizes quality and safety at every step.
OUR CAPABILITIES
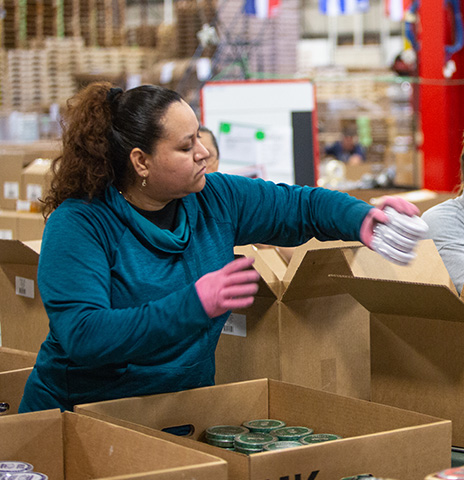
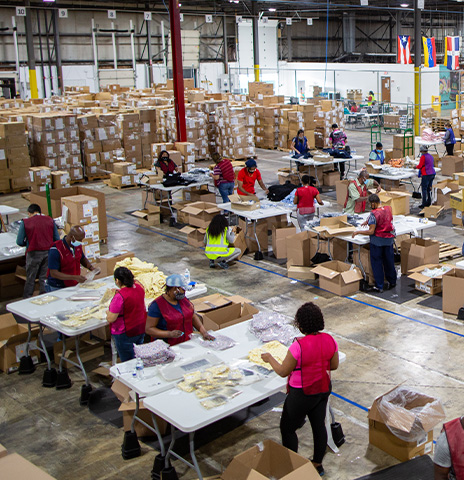
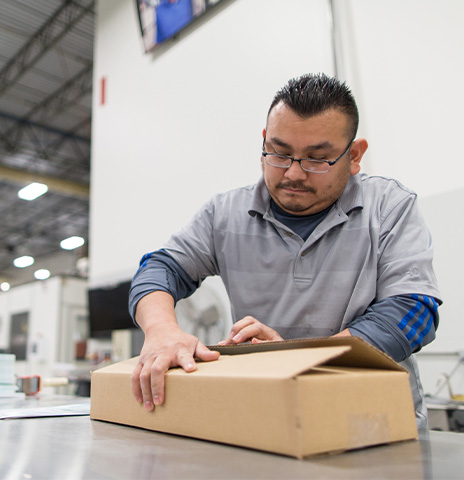
Fulfillment & Logistics Support
Improve efficiency and maintain client satisfaction by outsourcing key fulfillment operations. Our team leads will manage processes from pick and pack all the way to returns.
OUR CAPABILITIES
- Kitting and Assembly
- Primary and Secondary Packaging
- Shrink Wrap
- Labeling and Stickering
- Sortation
- Repack and Rework
- Display Builds
- Returns
- Refurbishing
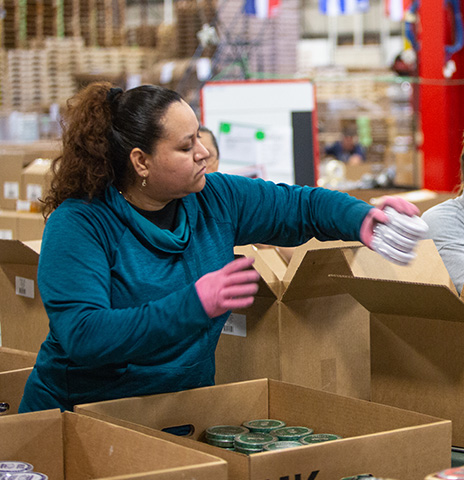
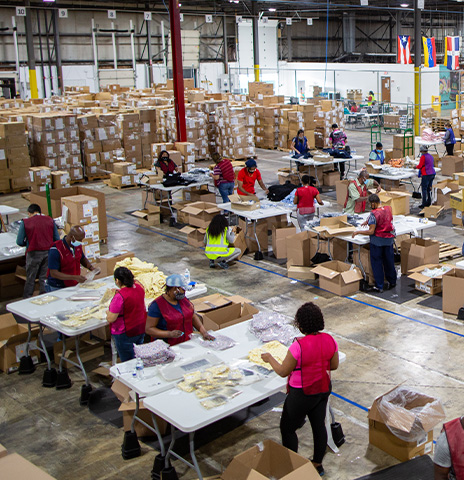
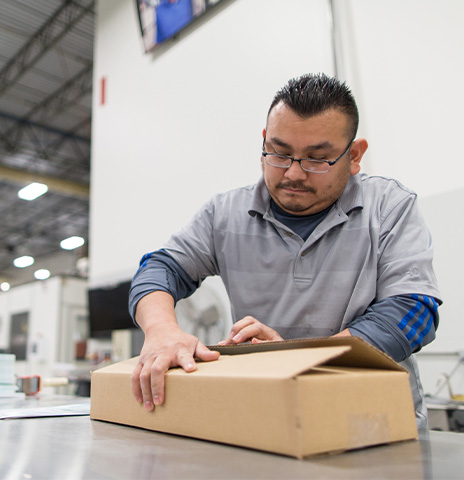
Fulfillment by Amazon (FBA) Prep
Ensure your products are properly packaged and sent on time for Fulfillment by Amazon. Acción Performance prepares your items to fit necessary requirements, saving your team extra time and valuable resources.
OUR CAPABILITIES
- Packaging Solutions
-
Packaging Solutions
Stay on top of product alterations and capitalize on packaging as a marketing tool to your clients. Our team can focus on product appearance while ensuring safe and secure delivery to its destination.
OUR CAPABILITIES
- Assembly &Co-Manufacturing Solutions
-
Assembly & Co-Manufacturing Solutions
Reduce overhead costs and boost speed to market by shifting your assembly and co-manufacturing tasks to the Acción team. Our skilled team prioritizes quality and safety at every step.
OUR CAPABILITIES
- Fulfillment &Logistics Support
-
Fulfillment & Logistics Support
Improve efficiency and maintain client satisfaction by outsourcing key fulfillment operations. Our team leads will manage processes from pick and pack all the way to returns.
<OUR CAPABILITIES
- Kitting and Assembly
- Primary and Secondary Packaging
- Shrink Wrap
- Labeling and Stickering
- Sortation
- Repack and Rework
- Display Builds
- Returns
- Refurbishing
- Fulfillment by Amazon (FBA) Prep
-
Fulfillment by Amazon (FBA) Prep
Ensure your products are properly packaged and sent on time for Fulfillment by Amazon. Acción Performance prepares your items to fit necessary requirements, saving your team extra time and valuable resources.
OUR CAPABILITIES
Our Capabilities
Don’t let capacity constraints keep you from reaching your operational goals. Acción Performance can quickly adjust our resources to get started on projects quickly, and exceed timeline expectations.
Managing Modern Solutions
Optimized supply chain solutions aren’t “one size fits all,” and neither are our pricing models. Our team
finds the best approach for your project to maximize your resources, including cost.
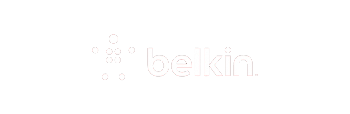
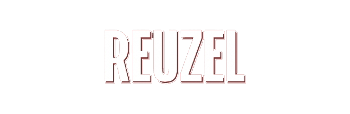
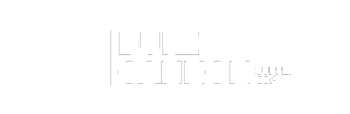
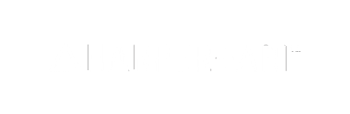
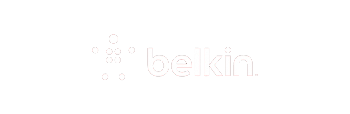
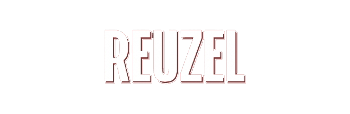
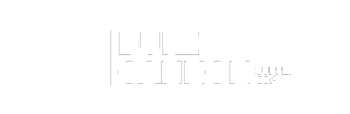
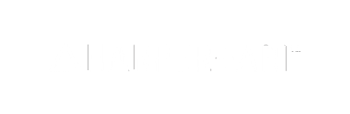
Custom Solutions
See how the Acción team creates individualized solutions for our clients across industries to optimize their unique demands.
Globally, millions of people shop online, then wait a day or two for the delivery. Meeting these one and two-day shipping obligations isn’t easy. The pick, pack and ship process can be complicated without the right systems in place. With careful logistics planning and modern AI technology, online marketplaces create pick, pack and ship deliveries that people rely on.
Behind the scenes, an army of warehouse workers diligently go from millions of packages to one or two packages. The pick-and-pack process in warehouse settings involves a dynamic logistical system where online marketplaces give consumers the shop from home convenience. Ever wonder what is pick and pack fulfillment? In simplest terms, it is the process of getting the right product into the right packing to meet the deadline. The fulfillment center is a key part of the buyer’s experience. Without smooth running systems and processes done by trained warehouse workers, the buyer’s experience would be negative, causing sales problems.
To facilitate accuracy and efficiency, the packing in warehouses and supply chains must adhere to specific guidelines so that the logistics don’t cause delivery backups. For example, the packing process must facilitate easy moving and stack in a pick-and-pack fulfillment center where the pick-and-pack process helps delivery drivers get packages out for delivery.
What is pick and pack fulfillment? Large online marketplaces use strategically placed warehouses where warehouse workers pick the requested products and then pack them in secure packaging for delivery. This pick, pack and ship process usually has some type of pick and pack fee added onto the delivery, not unlike a shipping and handling charge.
The packing process for independent e-commerce vendors usually requires a pick and pack fee to complete the pick, pack and ship obligation. Usually, computers and other devices connected to the internet have geolocation services. Independent sellers should use the “pick and pack near me” search string for the best results.
Packing Process In Warehouse
The packing process in warehouse situations is the first part of buyers’ journeys. When an online buyer puts something in their cart and makes a purchase, the buyer’s experience begins, often with some measure of impatience. Consequently, a picking process in warehouse settings that helps get packages delivered on time (or even early) helps the seller get good reviews. The right packing in warehouse settings makes delivering packages easier due to AI and logistics.
Download the packing procedure pdf and discover differences in the picking process in warehouse settings, which aren’t the same as going to a store and picking a product off a shelf. In contrast, the warehouse worker must pick products that help the shipping process in warehouse settings. Rules such as “first in fire out” must be automated so that deliveries are as fresh as possible. Both the picking and packaging processes must work together for customer satisfaction.
Large online marketplaces sometimes have a pdf packing procedure explaining the steps they use to deliver packages. Basically, the picking process in warehouse situations must help the supply chain work efficiently to maintain stable supply and demand. When these situations work, the shipping process in warehouse settings helps customers feel good about their purchases.
Types of Packing in Warehouse
There are three types of packing in warehouse situations, each of which must work together to facilitate delivering packages on time. These types of packaging – primary, secondary and tertiary – fit inside progressively bigger delivery and storage situations. For example, a big metal shipping container with several pallets of boxes full of one type of lipstick.
The progressively bigger types of packaging in logistics help warehouse workers process and sort bulk items, like a specific shade of lipstick, into individual packages for shipping. Warehouse workers pick and pack products, then other warehouse workers choose types of packaging materials that suit the shipping situation.
Picking and Packing In Warehouse
What is picking and packing? In a warehouse setting, workers must follow the picking and packing best practices established by management. This ensures the logistics behind shipping and handling run smoothly without interfering with delivery deadlines. This type of work is fast-paced and dynamic.
Pick, Pack Ship Process Flow
The pick, pack ship process flow in a fulfillment center helps warehouse workers get customers’ purchased products to them in the allotted time. Today’s e-commerce customers expect quick deliveries, making the picking and packing process in warehouse settings more important than ever. Only those pick, pack and ship services that fit into the logistical product delivery should make into a best practice list.
Pick and Pack Warehouse Meaning
Packing in warehouse settings should facilitate fast turnaround delivery rates. Something isn’t working in the workflow if they don’t speed things up. Thus, the pick-and-pack warehouse meaning is really an order fulfillment center like the many warehouses owned and run by Walmart and other large retailers.