Partnering with Acción Performance allows your business to remain agile as production needs shift. Our custom pick and pack fulfillment services eliminate wasted resources by optimizing performance as we seamlessly integrate into your logistics processes.
Pick and Pack Fulfillment Services
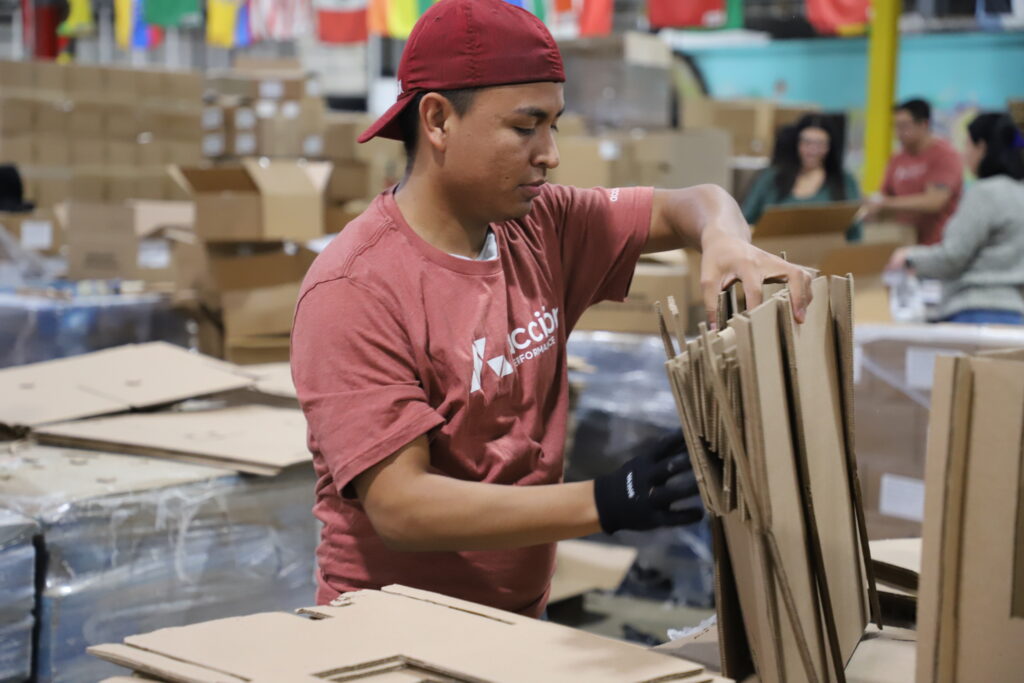
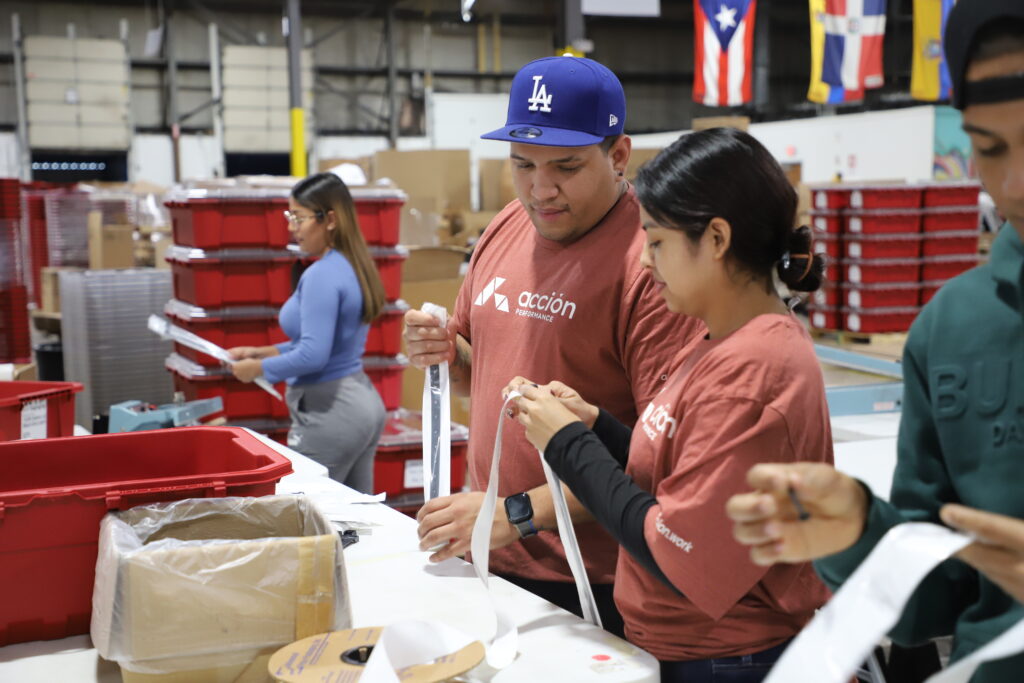
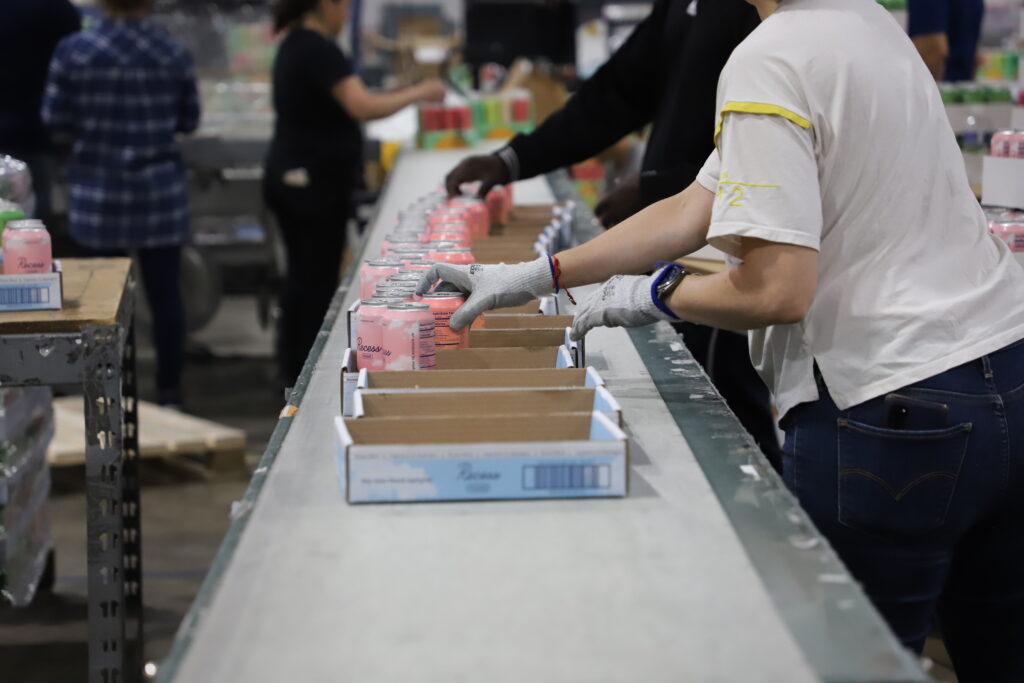
Packaging Solutions
Stay on top of product alterations and capitalize on packaging as a marketing tool to your clients. Our team can focus on product appearance while ensuring safe and secure delivery to its destination.
OUR CAPABILITIES
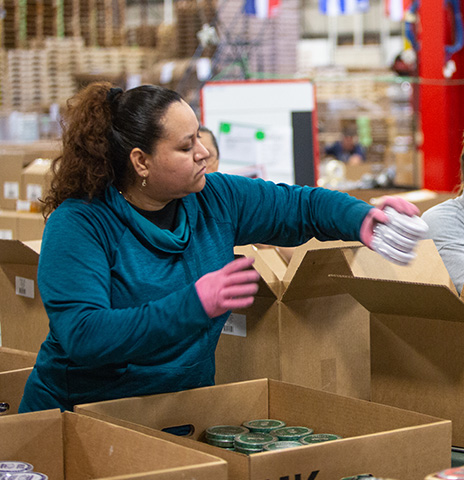
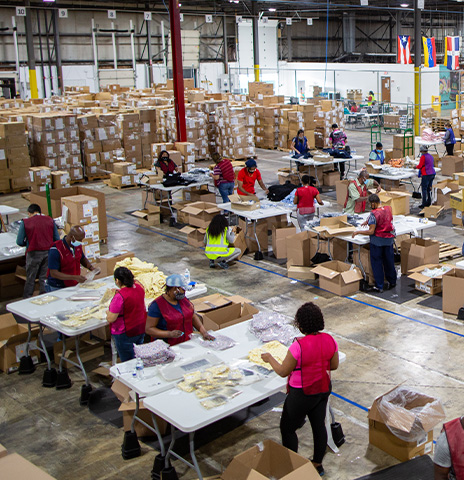
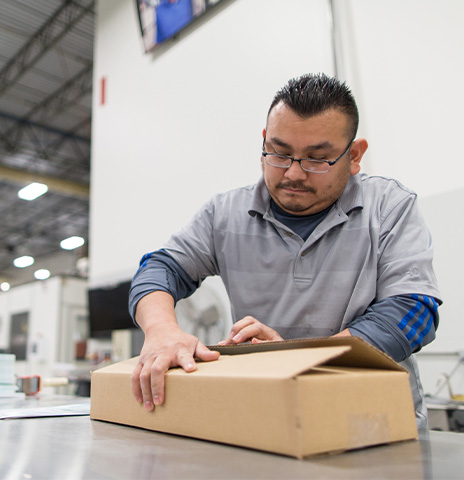
Fulfillment & Logistics Support
Improve efficiency and maintain client satisfaction by outsourcing key fulfillment operations. Our team leads will manage processes from pick and pack all the way to returns.
OUR CAPABILITIES
- Kitting and Assembly
- Primary and Secondary Packaging
- Shrink Wrap
- Labeling and Stickering
- Sortation
- Repack and Rework
- Display Builds
- Returns
- Refurbishing
- Packaging Solutions
-
Packaging Solutions
Stay on top of product alterations and capitalize on packaging as a marketing tool to your clients. Our team can focus on product appearance while ensuring safe and secure delivery to its destination.
OUR CAPABILITIES
- Fulfillment &Logistics Support
-
Fulfillment & Logistics Support
Improve efficiency and maintain client satisfaction by outsourcing key fulfillment operations. Our team leads will manage processes from pick and pack all the way to returns.
<OUR CAPABILITIES
- Kitting and Assembly
- Primary and Secondary Packaging
- Shrink Wrap
- Labeling and Stickering
- Sortation
- Repack and Rework
- Display Builds
- Returns
- Refurbishing
Our Capabilities
Don’t let capacity constraints keep you from reaching your operational goals. Acción Performance can quickly adjust our resources to get started on projects quickly, and exceed timeline expectations.
Managing Modern Solutions
Optimized supply chain solutions aren’t “one size fits all,” and neither are our pricing models. Our team
finds the best approach for your project to maximize your resources, including cost.
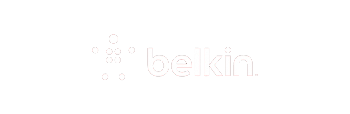
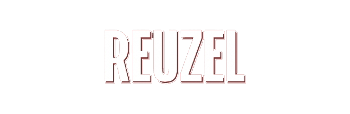
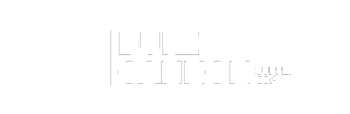
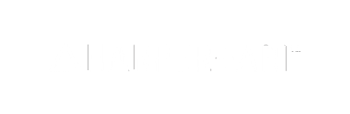
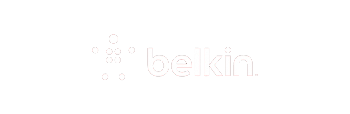
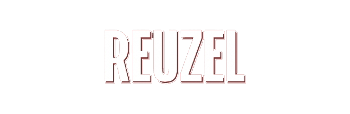
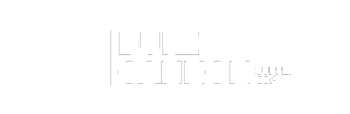
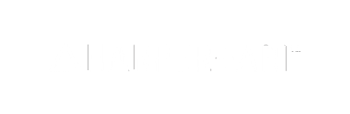
Custom Solutions
See how the Acción team creates individualized solutions for our clients across industries to optimize their unique demands.
Pick and Pack Fulfillment Services
Pick and pack fulfillment services refer to the process of pulling individual items from larger packages in warehouse shelves and repacking them into smaller boxes, envelopes or any other packaging according to the customer order. Picking and packing services are particularly important for retailers who receive small orders from various locations.
Pick and pack fulfillment services can take place in distribution or fulfillment centers. The primary difference between the two is the operations that occur in either. Although both facilities are customer centered, distribution centers serve B2B customers while most fulfilment centers act as third-party links between the retailers and direct customers.
Warehouse distribution companies charge pick and pack fees for having their employees prepare product for delivery. For example, amazon takes a pick and pack fee for having one of their workers search, choose, package, and prepare an item for delivery in the warehouse. The company also charges a weight handling fee, which is a fee charged per pound depending on the entire weight of the item to be shipped.
Amazon also subjects sellers to FBA (Fulfillment by Amazon) storage fees to cater for inventory. management. The standard 2022 FBA charge is $0.15 per unit or $6.90 per cubic foot depending on the type of master packaging or product. This is an extra charge typically imposed on inventory that has been in storage for over a year as it awaits sales.
Pick and Pack Process
The pick and pack process utilizes a repetitive procedure of collecting and ordering items from inventory or warehouse shelves and packing them according to order specifications for shipment. It is the first and most integral part of the order fulfillment process, thus accuracy is mandatory.
Different companies tend to personalize their pick and pack process to improve speed, efficiency and ultimately minimize the cost of handling inventory. The process entails locating and picking items accurately according to customer orders, then packing them securely using the necessary supplies to ensure the reach the final destination damage-free.
Companies have found innovative and efficient strategies to promote the process. They include:
· Piece picking- employees pick orders one at a time in the sequence of their reception. An order must be fulfilled before going to the next, to promote accuracy
· Batch picking-usually used by larger warehouses to promote smooth flow of order traffic. It involves picking items for more than one order at a time.
· Zone picking- the warehouse is divided into zones and pickers assigned to each zone. The workers are only allowed to pick items from their zones.
· Wave picking- combines zone and batch picking strategies whereby workers can pick multiple items for different orders but strictly within their zone
These strategies are helpful in developing best pick and pack practices thus promoting seamless running of operations in the distribution or fulfillment warehouse.
Pick, Pack and Ship Services
It is impossible to prepare and ship entire cases and pallets of goods. Most e-commerce retailers rely on workers for order fulfillment. The process is exactly as it sounds, where warehouse employees pick or collect the right items for specific order. The items are then packed into boxes before shipping which is basically transporting the ordered items to the customers.
Pick and pack services are reasonable options for small scale companies that cannot afford to own, rent or lease warehouses. This means that pick, pack and shipping services can be delivered by independent companies. These companies are more customer-centered and their primary role is to facilitate consumer satisfaction.
Pick, pack ship best practices also improve the ability of these companies to deliver quality services to their customers. Some of these practices include, keeping track of goods as they transit through the service chain, automating redundant processes to minimize errors and creating double checking mechanisms that are instrumental in catching mistakes before the products leave the warehouse.