Partnering with Acción Performance allows your business to remain agile as production needs shift. Our custom pick and pack service offerings eliminate wasted resources by optimizing performance as we seamlessly integrate into your logistics processes.
Pick and Pack Service
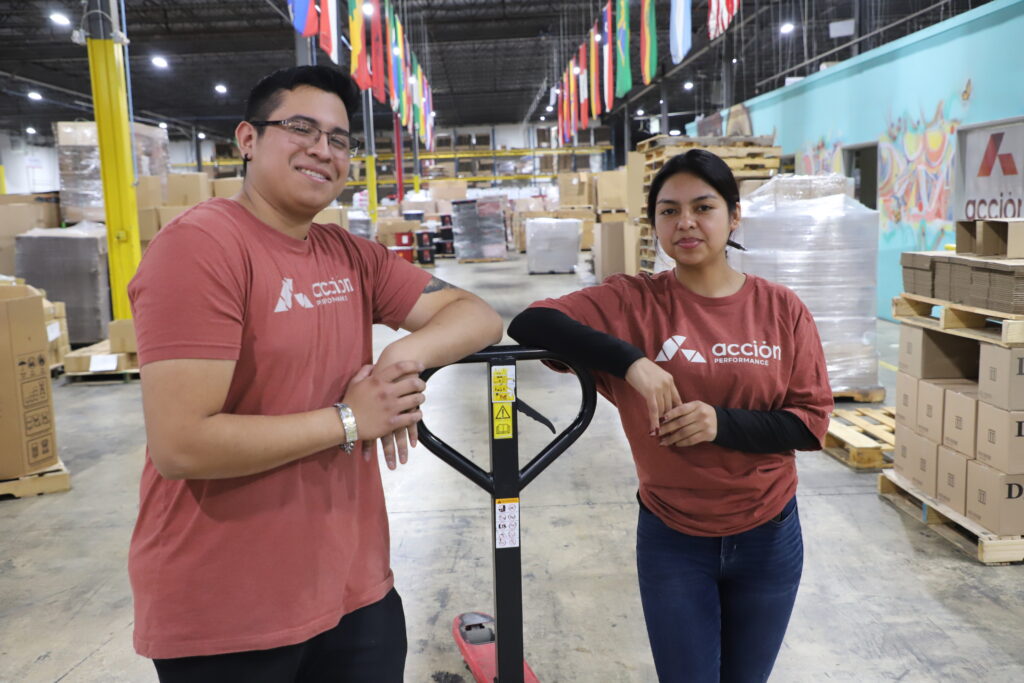
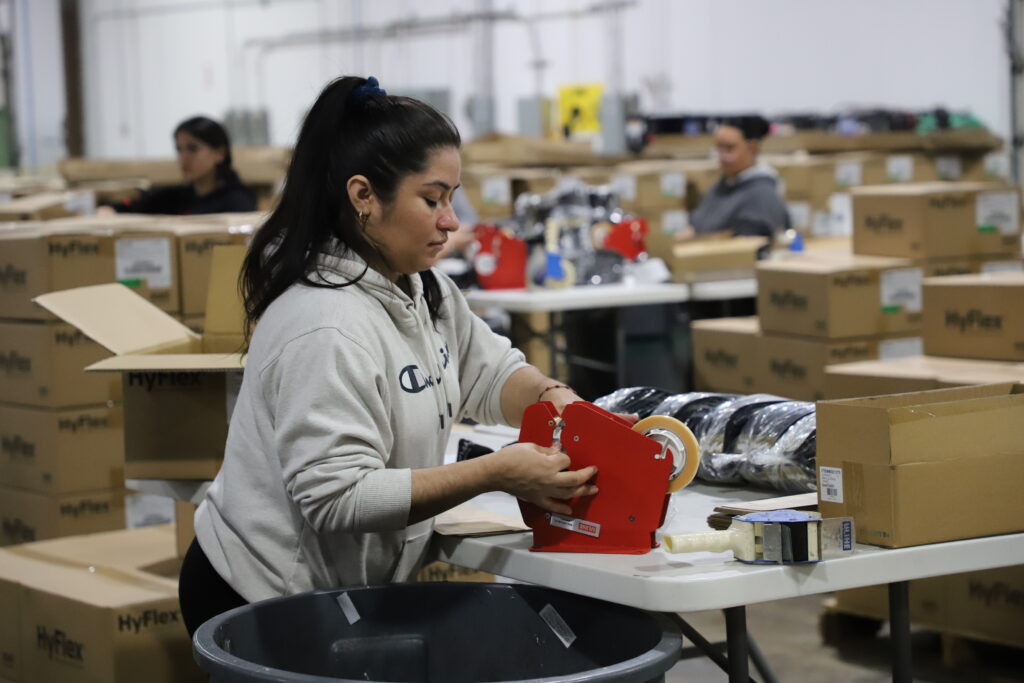
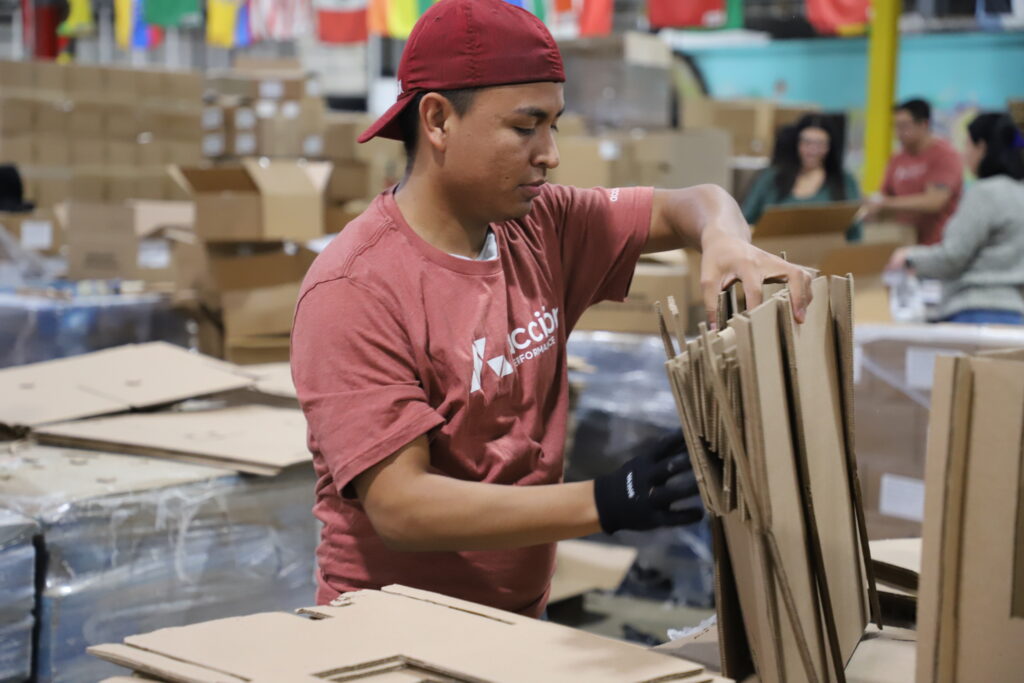
Packaging Solutions
Stay on top of product alterations and capitalize on packaging as a marketing tool to your clients. Our team can focus on product appearance while ensuring safe and secure delivery to its destination.
OUR CAPABILITIES
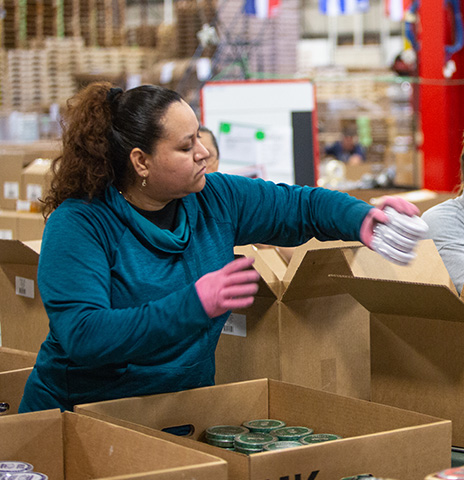
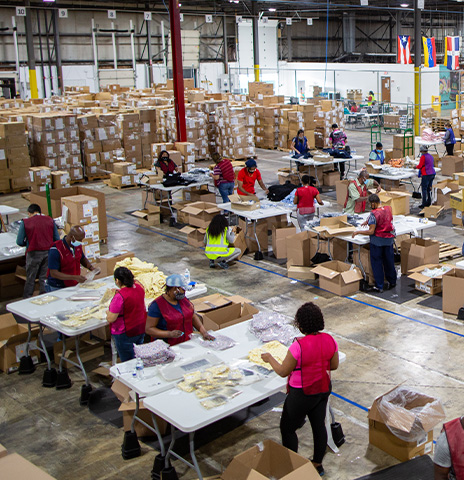
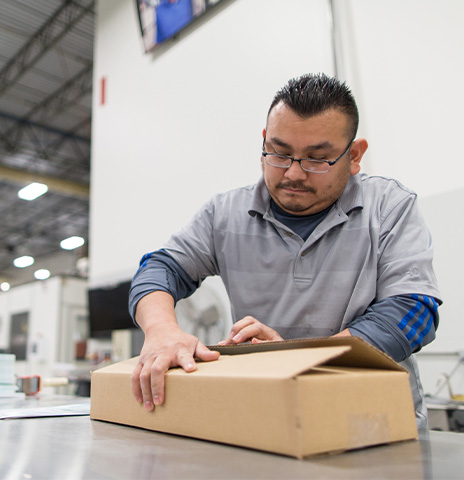
Fulfillment & Logistics Support
Improve efficiency and maintain client satisfaction by outsourcing key fulfillment operations. Our team leads will manage processes from pick and pack all the way to returns.
OUR CAPABILITIES
- Kitting and Assembly
- Primary and Secondary Packaging
- Shrink Wrap
- Labeling and Stickering
- Sortation
- Repack and Rework
- Display Builds
- Returns
- Refurbishing
- Packaging Solutions
-
Packaging Solutions
Stay on top of product alterations and capitalize on packaging as a marketing tool to your clients. Our team can focus on product appearance while ensuring safe and secure delivery to its destination.
OUR CAPABILITIES
- Fulfillment &Logistics Support
-
Fulfillment & Logistics Support
Improve efficiency and maintain client satisfaction by outsourcing key fulfillment operations. Our team leads will manage processes from pick and pack all the way to returns.
<OUR CAPABILITIES
- Kitting and Assembly
- Primary and Secondary Packaging
- Shrink Wrap
- Labeling and Stickering
- Sortation
- Repack and Rework
- Display Builds
- Returns
- Refurbishing
Our Capabilities
Don’t let capacity constraints keep you from reaching your operational goals. Acción Performance can quickly adjust our resources to get started on projects quickly, and exceed timeline expectations.
Managing Modern Solutions
Optimized supply chain solutions aren’t “one size fits all,” and neither are our pricing models. Our team
finds the best approach for your project to maximize your resources, including cost.
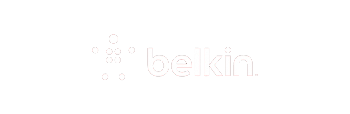
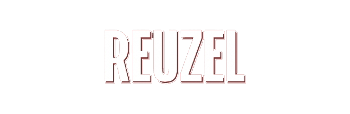
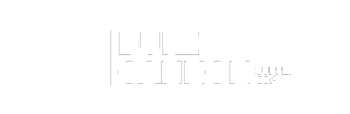
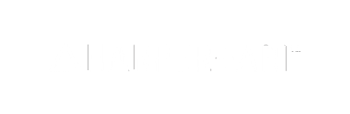
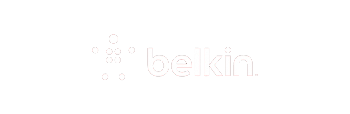
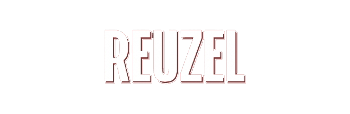
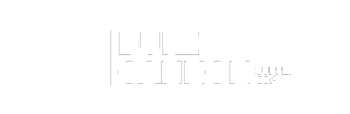
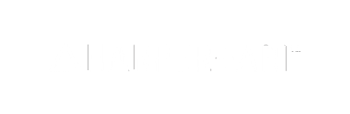
Custom Solutions
See how the Acción team creates individualized solutions for our clients across industries to optimize their unique demands.
A pick and pack service is essential to inventory management and product fulfillment, whereby warehouse workers pull out individual items from entire cases of goods or master cartons. They pack the items in smaller boxes or envelopes for specific customers according to their orders. The entire pick and pack process is necessary for accurate inventory keeping and to ensure timely shipment and delivery of items.
Pick and pack activities take place in a warehouse, thus extending the purpose of a warehouse beyond storage. Modern warehouses serve numerous functions, including serving as supply chain data centers. This is possible because items are collected and distributed from the storage facilities, thus making them the perfect stations to handle information vital to manufacturers and distributors.
In a nutshell, the three primary benefits of warehouses include: they act as storage for surplus goods, minimize the risk of damage to products and offer better security to data and items. Warehouses are also socially beneficial as they employ so many people.
Pick, and packing requires elaborate systems often designed to align with the needs of different customers and the nature of their products. That often means that companies will offer different types of packing techniques, thus, different packing materials.
Types of Packing in a Warehouse
There are three levels of packaging which include:
- Primary Packaging
This type of packaging is meant for the products headed directly for the point-of-use or end-user. The products are usually in consumer units, and the primary function of the packaging is to protect the product from contamination. An example of Primary packaging is whole-grain cereal stored in a plastic container.
- Secondary Packaging
Secondary packaging is the second layer whereby one box or case holds smaller units of products—for example, a cardboard box holding several jars of jelly.
- Tertiary Packaging
Tertiary packaging is bulky and is used to hold several collections of SKUs, usually in secondary packaging. This type of packaging is used to help in the large-scale transportation of items from one point to the other.
Picking and Packing warehouses break down the tertiary packages into secondary or primary packages.
What is Pick and Pack Fulfillment?
Pick and pack fulfillment is a vital process that entails various steps necessary to prepare an order in readiness for shipment and delivery. As the name suggests, it includes picking and packing activities whereby a warehouse worker physically picks an item from a group of many shelves and packs them into a different packaging according to the order.
Generally, the fulfillment process begins when a customer orders. The role of fulfillment packing is to ensure the client can satisfy the order by receiving, packing, and shipping them appropriately. As the products are collected manually, they are allocated a new SKU number and recorded for accurate inventory keeping.
Picking on its own requires a high level of attention as the worker must collect the right type and number of items from the shelf to avoid errors that could easily compromise the quality of the entire supply chain. Most prominent businesses, like large-scale manufacturers, own private pick and pack warehouses and charge clients pick and pack fees separately. However, others, including ecommerce stores that cannot afford private warehouses, often rely on third-party logistics companies whose role is to satisfy customers’ orders and transport them to their final destinations.
Pick, Pack, and Ship
A complete fulfillment service can be summarized into three fundamental steps- picking, packing, and shipping. Here is an overview of what happens at each stage:
- Picking
Workers, or pickers, have lists or are allocated orders at this stage. Using these orders as a reference, they source the products from large batched or warehouse shelves. As the pickers select these items, a warehouse clerk keeps track of the inventory.
Typically, pickers are allocated orders or picking stations according to the order’s magnitude or the brand’s size. The warehouse may be divided into zones to optimize the search and enhance accountability.
- Packing
Once the products are picked, they are taken to the packing station, where they are gathered for packing. During this step, items can be separated according to packaging and labeled. Some orders may be grouped to form kits which are necessary to create a complete product through a process known as kitting. Kitting is gathering individual components into a single unit.
- Shipping
The last step after the items are picked, packed, and labeled is ensuring they get to the point of use- shipping. Once the packages are sent out, businesses and their clients rely on automated tracking systems, which optimize the process by instilling trust through transparency.
These steps make up the basic protocols for most fulfillment service providers, and the quality of fulfillment service depends on the maximization of proper warehouse practices at each stage.
Pick and Pack Amazon
Amazon is a popular name in the ecommerce business, offering different products to retail and wholesale buyers. Like any other ecommerce business, Amazon offers to pick, pack, and ship services to satisfy customer orders. With a brand of their magnitude, it makes sense to outsource these services. However, Amazon also offers other businesses fulfillment services through their child company, Fulfillment by Amazon.
Fulfillment by Amazon allows businesses to send products via Amazon fulfillment centers, usually spread out across different states across the United States and Internationally. The service includes picking, packing, shipping, and processing order returns.
FBA offers an incredibly straightforward process for beginners with clear outlines on how to get started on their website. These steps include:
- Setting up an FBA or Amazon selling account
- Creating product listings by adding products to the amazon inventory
- Preparing your products for secure transportation
- Shipping the products to Amazon warehouses.
FBA allows people to become online Amazon sellers. Sellers only have to pay amazon fba fees to put products on the marketplace. The fba pick and pack fees are charged on every unit sold. The platform also offers members tools like the FBA revenue calculator to help them calculate and understand the fba fees.
Pick and Pack Process
The pick and pack process often sounds very straightforward; however, it is detrimental to a company’s supply chain. Retrieving orders, picking, labeling, and packing requires a high level of organization. Pick and pack service providers continue to innovate ways to aid the process and reduce the chances of errors.
These techniques include adopting different types of pick and packing methods, such as:
- Piece picking involves selecting one item at a time and isolating them from one order after the other.
- Batch picking- collecting orders in groups and packing them simultaneously. This method works well when the products are similar.
- Zone picking involves dividing the warehouse into zones and temporarily assigning workers to these divisions so that they only pick and pack at specified stations.
Pick and pack companies may also improve their services using automated systems. Unlike manual systems, automated systems integrate or solely rely on softwares and machines to process orders. The systems recognize customer orders and suggest the appropriate package sizes. Others proceed to suggest and allocate shipping methods to orders automatically. These techniques help create the best picking and packing practices for seamless order fulfillment.