Partnering with Acción Performance allows your business to remain agile as production needs shift. Our custom picking and packing services eliminate wasted resources by optimizing performance as we seamlessly integrate into your logistics processes.
Picking And Packing Services
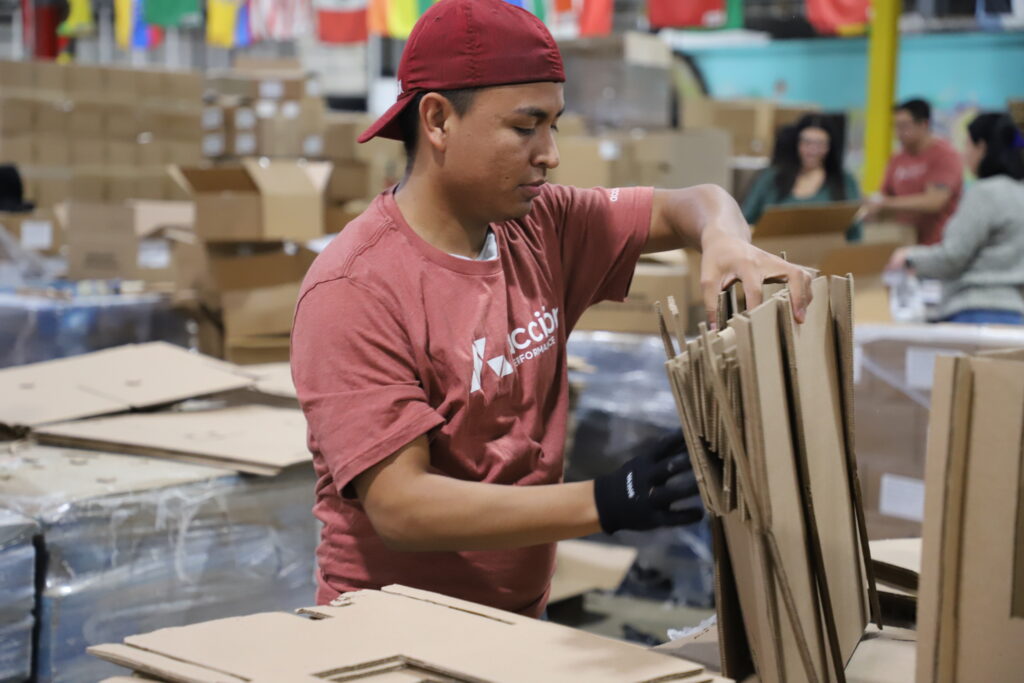
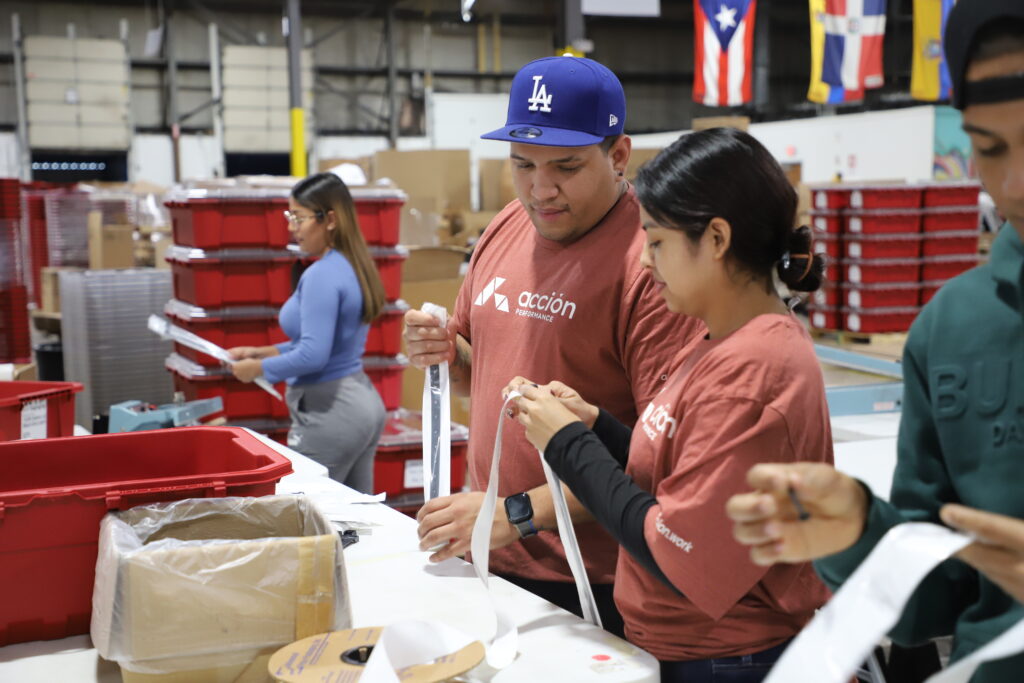
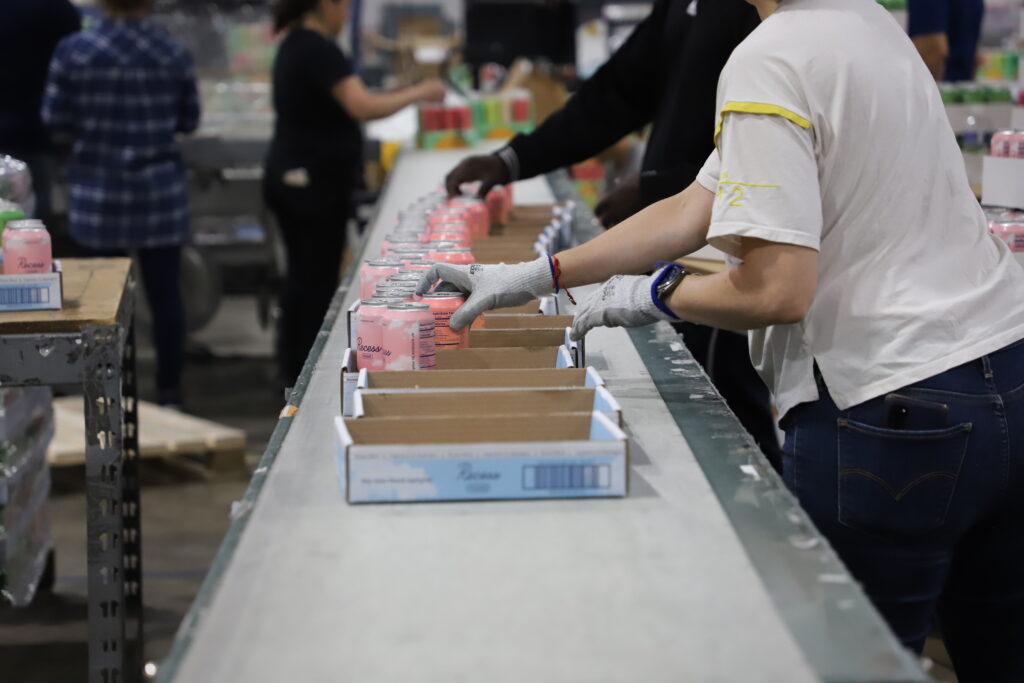
Packaging Solutions
Stay on top of product alterations and capitalize on packaging as a marketing tool to your clients. Our team can focus on product appearance while ensuring safe and secure delivery to its destination.
OUR CAPABILITIES
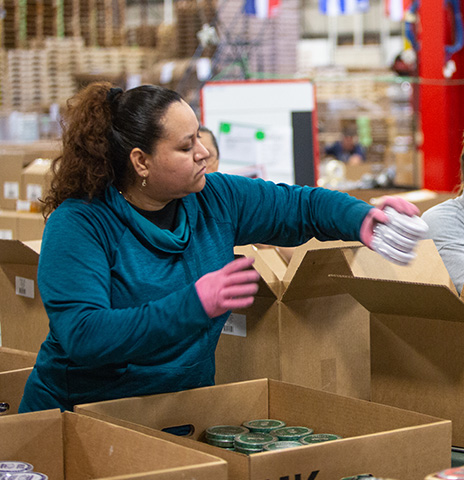
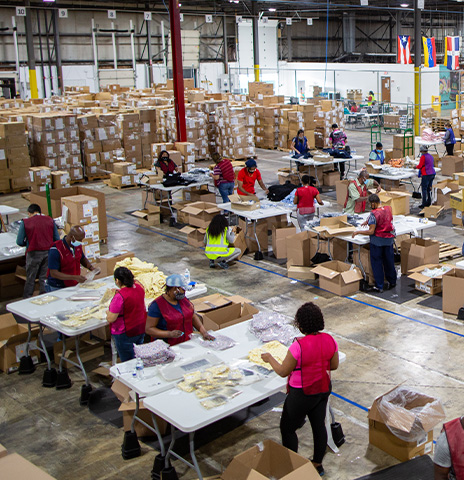
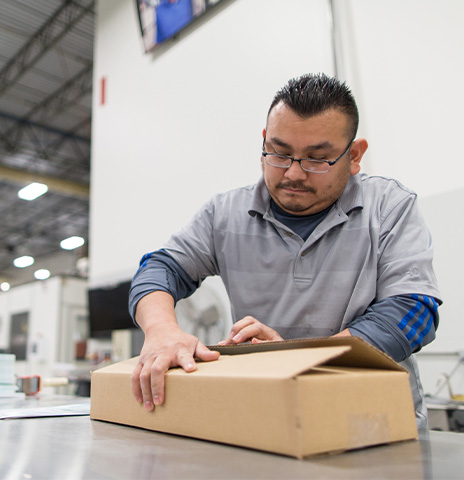
Fulfillment & Logistics Support
Improve efficiency and maintain client satisfaction by outsourcing key fulfillment operations. Our team leads will manage processes from pick and pack all the way to returns.
OUR CAPABILITIES
- Kitting and Assembly
- Primary and Secondary Packaging
- Shrink Wrap
- Labeling and Stickering
- Sortation
- Repack and Rework
- Display Builds
- Returns
- Refurbishing
- Packaging Solutions
-
Packaging Solutions
Stay on top of product alterations and capitalize on packaging as a marketing tool to your clients. Our team can focus on product appearance while ensuring safe and secure delivery to its destination.
OUR CAPABILITIES
- Fulfillment &Logistics Support
-
Fulfillment & Logistics Support
Improve efficiency and maintain client satisfaction by outsourcing key fulfillment operations. Our team leads will manage processes from pick and pack all the way to returns.
<OUR CAPABILITIES
- Kitting and Assembly
- Primary and Secondary Packaging
- Shrink Wrap
- Labeling and Stickering
- Sortation
- Repack and Rework
- Display Builds
- Returns
- Refurbishing
Our Capabilities
Don’t let capacity constraints keep you from reaching your operational goals. Acción Performance can quickly adjust our resources to get started on projects quickly, and exceed timeline expectations.
Managing Modern Solutions
Optimized supply chain solutions aren’t “one size fits all,” and neither are our pricing models. Our team
finds the best approach for your project to maximize your resources, including cost.
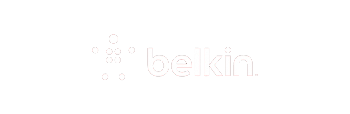
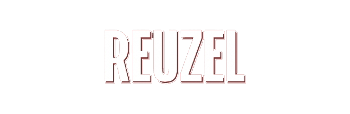
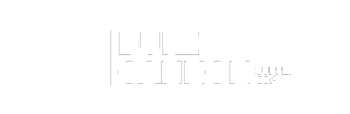
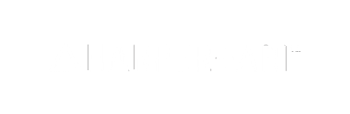
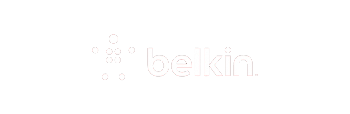
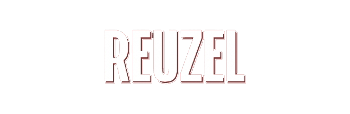
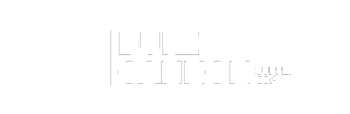
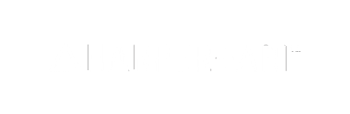
Custom Solutions
See how the Acción team creates individualized solutions for our clients across industries to optimize their unique demands.
Picking and Packing Services
Looking for a ‘pick and pack’ near me? Having a timely and accurate picking and packing services process is essential if running a business online. It ensures that you get the correct orders to customers on time. More satisfied customers are better for your business.
Managing shipping orders takes up a lot of time. Pick and pack companies handle your order fulfillment services so that you can focus on the aspects of your business that you love. Orders get packed according to your needs and instructions. This arrangement works well for new and growing businesses.
When you work with picking and packing services, they handle extra fees and regulations when shipping goods abroad. It means that you can expand your business into new markets. Offering next-day delivery services to customers makes all the difference when it comes to e-commerce.
It is also possible to ship items on the same day, which is difficult for business owners to handle logistics by themselves. Pick and pack companies are a convenient way to outsource logistics management for people who operate online businesses.
Moving
Moving is often a hassle. Most people don’t move too much, so it can get complicated to figure out the dynamics of transporting things to a different location. Whether you are moving across the country, across town, or even between floors in the same building, it is prudent to seek full service moving near me.
A mover service makes the process much faster and more efficient. Get two men and a truck quote to have your items moved to your new home.
Moving crews handle loading and unloading, arranging of furniture, and delivery services. If you don’t have time to pack or unpack, you don’t have to worry. Private movers like the man with a truck near me will do it for you. They even dismantle and reassemble furniture.
Private movers can also store furniture and other items in a safe place while you finalize paperwork and other details on your new address. If you have any valuables or precious items you want to be transported, you can rest assured that all service movers will ensure your products for their safety.
They take the stress out of moving, doing all the heavy lifting so you can focus on what matters most.
Pack And Ship
Want to ship fragile or oversized items? Do you want custom packaging for particular items? If you answered yes to either of these questions, then a pack and ship company is what you are looking for.
What is pick and pack? The pick and pack definition is a fulfillment process that lets customers receive goods they ordered online. Not all mail carriers or moving companies offer these specialized services, especially for luxury items such as art, antique furniture, jewelry, and other items of sentimental value.
Standard shipping and moving companies can get a little rough with your goods, leaving you with damaged items and emotional distress. It is frustrating to wait for days, weeks, or months only for something to arrive in poor condition.
Amazon Fulfillment Center Nashville
Pick and pack fulfillment involves two things. First is picking, when employees use a list to trace each product back in the inventory. Some customers may order more than one item, so the quantity of orders gets checked and selected for accuracy. The second part is packing. Items get packed in the right boxes before being shipped from the pick and pack fulfillment center to the end destination.
These orders get placed together with others going to the same place. It streamlines the process. The picking and packing job description is a simple one. A worker, called a pick packer, goes through the inventory of a pick and pack fulfillment center, picking up all the items on the inventory list.
They ensure that the proper orders go to the right customers in the right quantities and on time.
Pick And Pack Warehouse
A lot goes into the picking and packing process in the warehouse. Understanding how this works determines the total costs associated with order fulfillment. The core of it is this: the more orders get processed and fulfilled, the lower the overall cost of fulfillment.
As stated in the earlier pick and pack warehouse job description, employees at the warehouse handle the logistics so that customers can receive the products they ordered on time.
Types Of Packing In Warehouse
There are several ways in which the pick, and pack process gets carried out:
1. Zone Picking And Packing
This is fast becoming the most popular pick and pack process for order fulfillment. It keeps employees in the exact location, which cuts down on time spent traveling. This way, employees only pick up goods in their area before passing them onto the next destination. If inventory lists have products from different zones, then items get moved by robots, tubes, or conveyor belts.
Zone picking and packing have the advantage of minimizing costs. However, the downside is that handling orders from multiple zones become tedious.
2. Piece Pick And Pack
This is the easiest method. A pick and pack employee goes through an inventory list, completing all products on that list. Upon completion, they move on to the following order. This method is suitable for smaller warehouses. In a large warehouse, such a process would take up a lot of time.
Pick and pack employees might have to cover miles on foot, walking from one end of the warehouse to the other. That is valuable time going to waste, leading to considerable delays in the order fulfillment process.
3. Batch Picking And Packing
With batch picking and packing, employees work on multiple lists simultaneously. It is more efficient. However, it makes accuracy more difficult. More than one customer may order the same item, which means the pick and pack employee only has to visit that area of the warehouse once. But the employees must remember that there are multiple lists to attend to at the same time. It places them at risk of losing track of orders.
4. Wave Picking And Packing
This is a twist on zone picking and packing. Rather than employees staying in one area of the warehouse working on one list, they handle multiple lists at a go. It is a more efficient version of order fulfillment.
Pick And Pack Process
The pick and pack process flow collects items ordered from the inventory and packs them for shipment to the customer. An organized and efficient pick and pack process flow are essential to any e-commerce business as it ensures customer satisfaction. When customers know that they will get their orders on time and in good condition, they trust online businesses.
Businesses with a perfect or near-perfect order rate always enjoy tremendous success over their competitors. This process begins with locating the items in the warehouse and picking them most accurately. Afterwards, the items get packed securely to ensure they are secure. Finally, the items get shipped to the customer.
This process sounds simple, but one of the biggest problems with the order fulfillment sector is delays between placing orders and delivering them. More customers and businesses continue moving towards online retail, and they want assurance that their orders will get fulfilled as quickly and efficiently as possible.
It means that all e-commerce businesses must make a solid pick and pack process flow as part of their structure into the future. Good quality order fulfillment services make for good PR and advertising. They keep online businesses ahead of the competition.
Pick And Pack Store
Warehousing Pro LLC offers order fulfillment services for e-commerce businesses and online stores across the United States. Their clients range from the most prominent firms to the most minor family-owned and run businesses. Warehousing Pro LLC has dedicated itself to delivering the best possible customer service.
All orders get treated with care and diligence, always arriving on or even ahead of schedule. The storage facility located in Nashville, TN, serves the whole country and its professional pick and pay staff.
Free Order Picking Software
Warehouse pick and pack software streamlines operations. They help boost efficiency, increase the visibility of your brand and maximize the resources you have available. There are several systems involved when it comes to warehouse pick and pack software, including:
1. Labor Management Systems
This software measures the hours spent on labor and tasks by ‘pick and pack’ warehouse employees. With this information, you can find ways to make your employees more productive and improve resource allocation.
2. Order Management Systems
All data regarding orders gets compiled under one system. This consolidation of data streamlines the processing of orders.
3. Inventory Management Systems
Instead of physically keeping track of your stock, inventory management systems monitor them for you. They are accurate and monitor the entire inventory of a warehouse.
Pack And Ship Software
Using pack and ship software is one of the picking and packing best practices. These applications allow you to minimize shipping times, save on expenses and terminate errors. For example, if you have warehouse storage in Nashville, pack and ship software would help you pack items with greater accuracy.
This software also solves problems you may encounter with processing orders, employee productivity, and complying with the requirements of retailers.
Here are some benefits of pack and ship software:
- Faster printing of shipping labels
- Improved order fulfillment
- Scaling of standardized packing and shipping procedures
- Processing of large orders in less time
- Automatic scaling to accommodate spikes in demand