Collaborating with Acción Performance enables your business to maintain its agility amidst changing production demands. Our custom kit assembly services enhances resource efficiency by optimizing performance, seamlessly integrating into your logistics operations to form an invaluable outsourced kitting solution.
Kitting Services
Our Supply Chain Solutions
Partnering with Acción Performance allows your business to remain agile as production needs shift. Our customized solutions eliminate wasted resources by optimizing performance as we seamlessly integrate into your logistics processes.
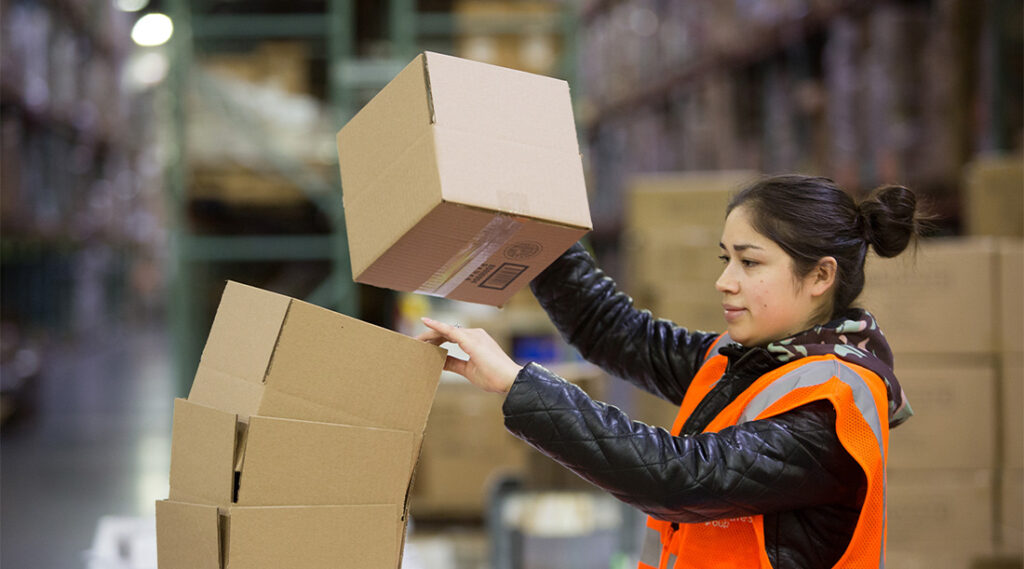
Kitting and Assembly Solutions
When you own a firm, supplying products to your customers requires various essential components such as packaging, distribution, and inventory management. It can be a bugbear if you tackle all the services yourself and everything else you have to do as a business owner. Fortunately, investing in a reputable company either for on-demand or pre-assembly kitting services for your business will get things done more successfully.
You can benefit from kitting in warehouse management if you own an e-commerce firm selling ready-to-assemble items, combination packs, subscription boxes, etc. Included in our kitting services, Acción Performance will store the products in our warehouses for our customers, eliminating the burden of renting a secondary space.
How We Solve Your Kitting and Assembly Problems
Acción Performance offers industry-leading turnaround times with a commitment to on-time delivery, ensuring your supply chain runs smoothly without delays. Our fast, reliable kitting services keep your business moving and your customers happy.
Acción Performance transparent pricing model eliminates hidden costs. We offer scalable, cost-effective kitting solutions that protect your margins while delivering superior service.
Acción Performance provides flexible, fully customizable kitting options that allow you to tailor kits to your exact specifications. From specialized components to unique packaging, we help you create a distinct, differentiated product experience.
Acción Performance grows with your business, offering scalable kitting solutions designed to handle increasing volumes and complexity. Whether small batches or large-scale operations, we’re ready to meet your demands without disruption.
Acción Performance prioritizes clear, proactive communication, offering dedicated account managers and real-time updates to eliminate miscommunication. With us, you get transparency at every step, ensuring your kitting requirements are met without errors.
Acción Performance delivers reliable, consistent kitting services, backed by a track record of error-free execution and on-time delivery. Our commitment to quality ensures your customers receive well-packaged, accurate orders every time.
Acción Performance supports your company through logistics coordination to ensure smooth handoffs, faster shipping, and reduced costs. Our support helps your kits arrive on time and intact, without logistical headaches.
Acción Performance adheres to the highest industry-specific regulations, ensuring your kits – are compliant and properly handled. Rest easy knowing your products meet all legal and safety requirements.
Acción Performance gives you full control and visibility over your kitting process with real-time tracking and detailed reports. Our transparent operations ensure you’re always in the loop, maintaining the standards and oversight you expect.
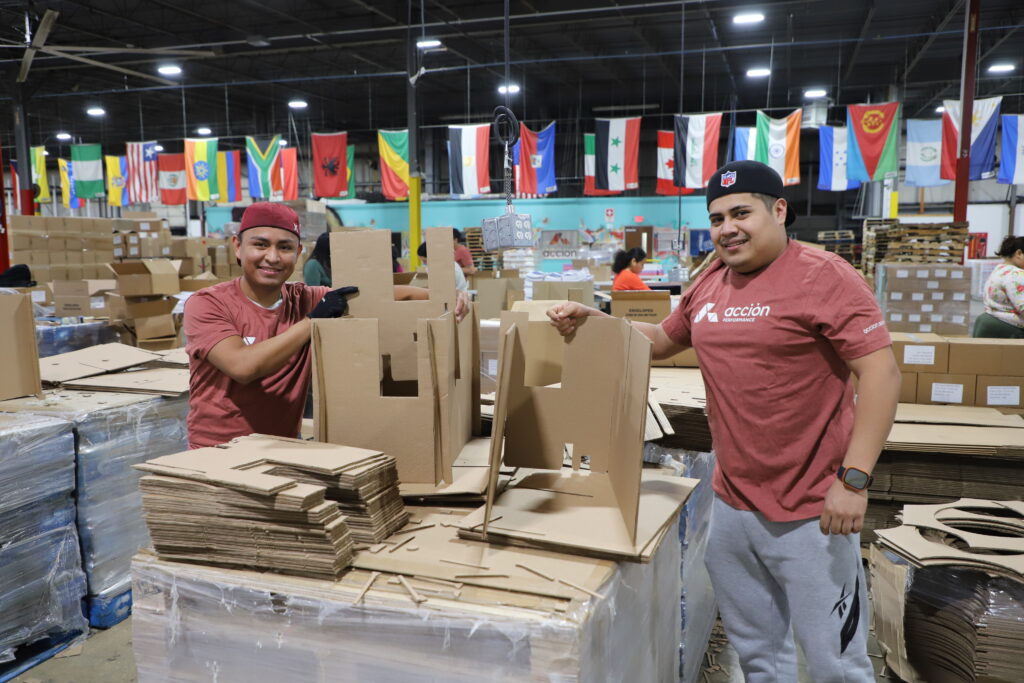
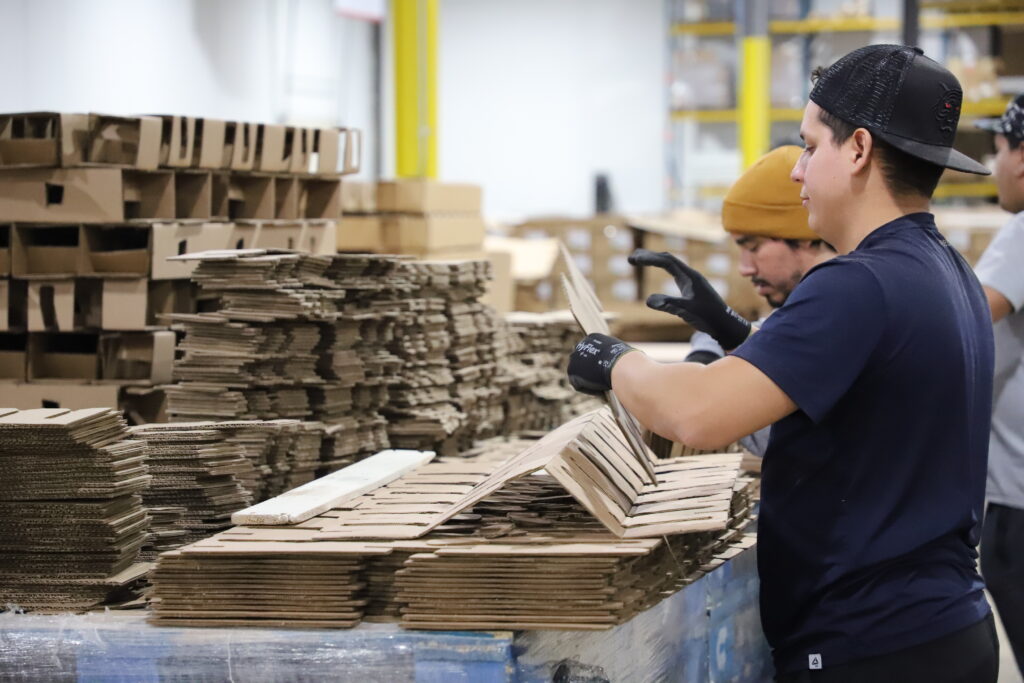
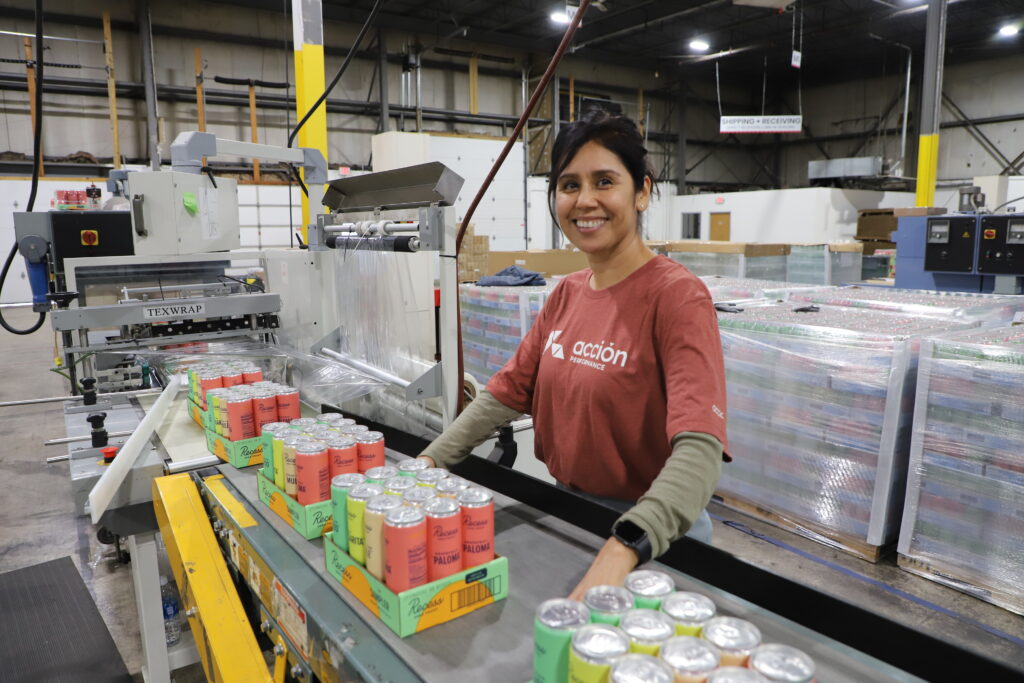
Packaging Solutions
Stay on top of product alterations and capitalize on packaging as a marketing tool to your clients. Our team can focus on product appearance while ensuring safe and secure delivery to its destination.
Managing Modern Solutions
Optimized supply chain solutions aren’t “one size fits all,” and neither are our pricing models. Our team
finds the best approach for your project to maximize your resources, including cost.
Custom Solutions
See how the Acción team creates individualized solutions for our clients across industries to optimize their unique demands.
Solutions Where You Need Them
We understand business needs from all industries. Our team is equipped to work when and where you need us.
Insourcing
Extend Your Capabilities:
Unlock the power of seamless integration as our expert team integrates directly into your facility. We bring specialized skills, adaptability, and unparalleled expertise right to your doorstep.
Adaptive Solutions:
Every facility has unique needs. Our team is trained to quickly adapt to diverse environments, ensuring a smooth transition and immediate productivity.
Assured Quality & Compliance:
Our team is trained to adhere to the highest standards of quality and compliance. Working within your facility, we’ll uphold and reinforce your brand’s reputation for excellence.
Outsourcing
Harness Our Team’s Skills:
Bring your projects to our facility, and our dedicated team will handle them with unmatched precision and skill. We offer a harmonious blend of your vision and our executional brilliance.
Seamless Integration:
Our team swiftly adapts to your specific requirements and methodologies, ensuring a seamless transition and continuity in your project outcomes.
Optimized Outcomes:
Our team, seasoned in diverse projects, ensures that your tasks are executed with efficiency, accuracy, and a commitment to the highest quality standards.
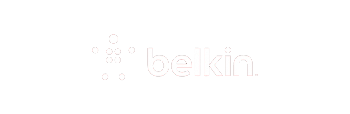
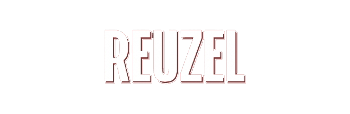
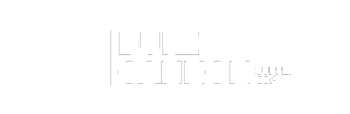
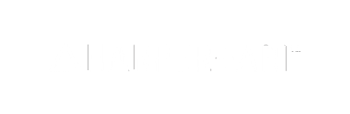